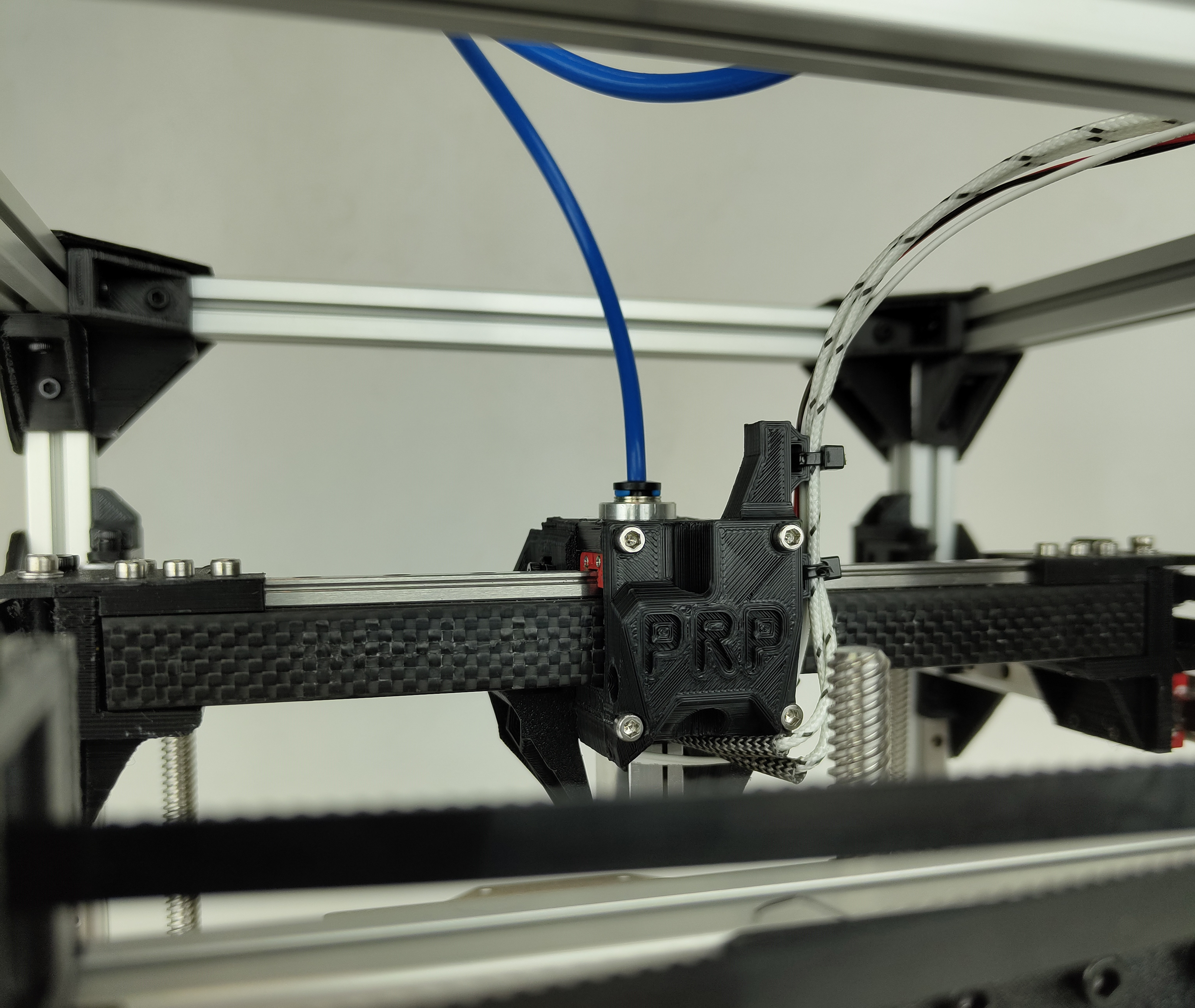
This project came from fustration, it was an idea to
make something that at the time didnt exist. A user
friendly, safe, portable, domestic, desk top use 3d
printer kit.
make something that at the time didnt exist. A user
friendly, safe, portable, domestic, desk top use 3d
printer kit.
This naturally is easier said than done, so I asked
alot of questions, talked to many people who
are far more knowledgeable than me and spent
many sleepless nights worrying about it.
tHE CULMINATION OF THIS WORK IS SHOWN BELOW IN THE FORM OF A FUNCTIONING SAFE 3d PRINTER KIT AND PROCESS OF MAKING IT.
One of the biggest issues I identified was around the creation of dangerous Voc's and particulate that has been found to be carcinogenic.
One of the key things that helped with project was the information in the paper "Characterization of Volatile and Particulate Emissions from Desktop 3D Printers", it helped hugely in finding the direction for this project.
“ABS recovered abundances of the three highest emitters–styrene, isophorone, ethylbenzene–for each filament. All these compounds are listed as possible human carcinogens under the IARC”
One of the key aims of this printer was to implement the filtratrion systems that are being ignored by mass manufacturers.
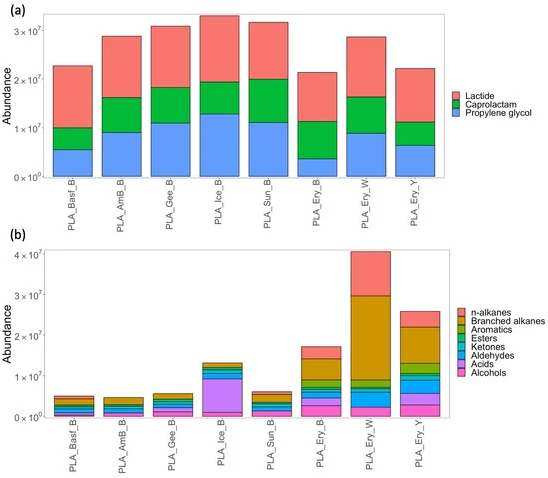
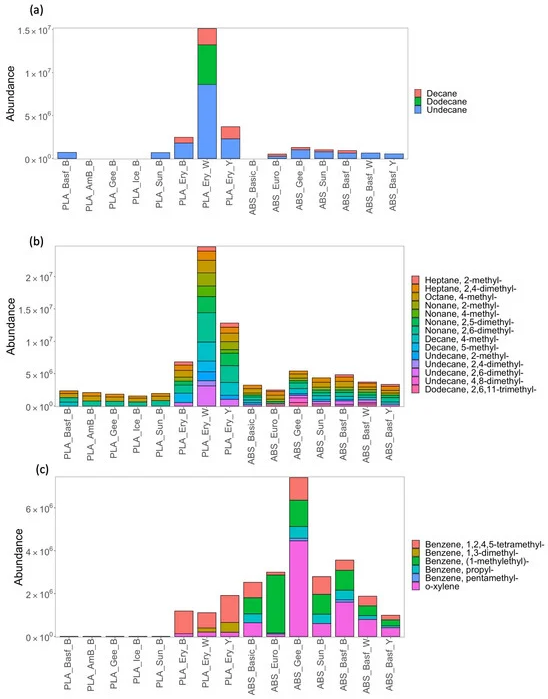
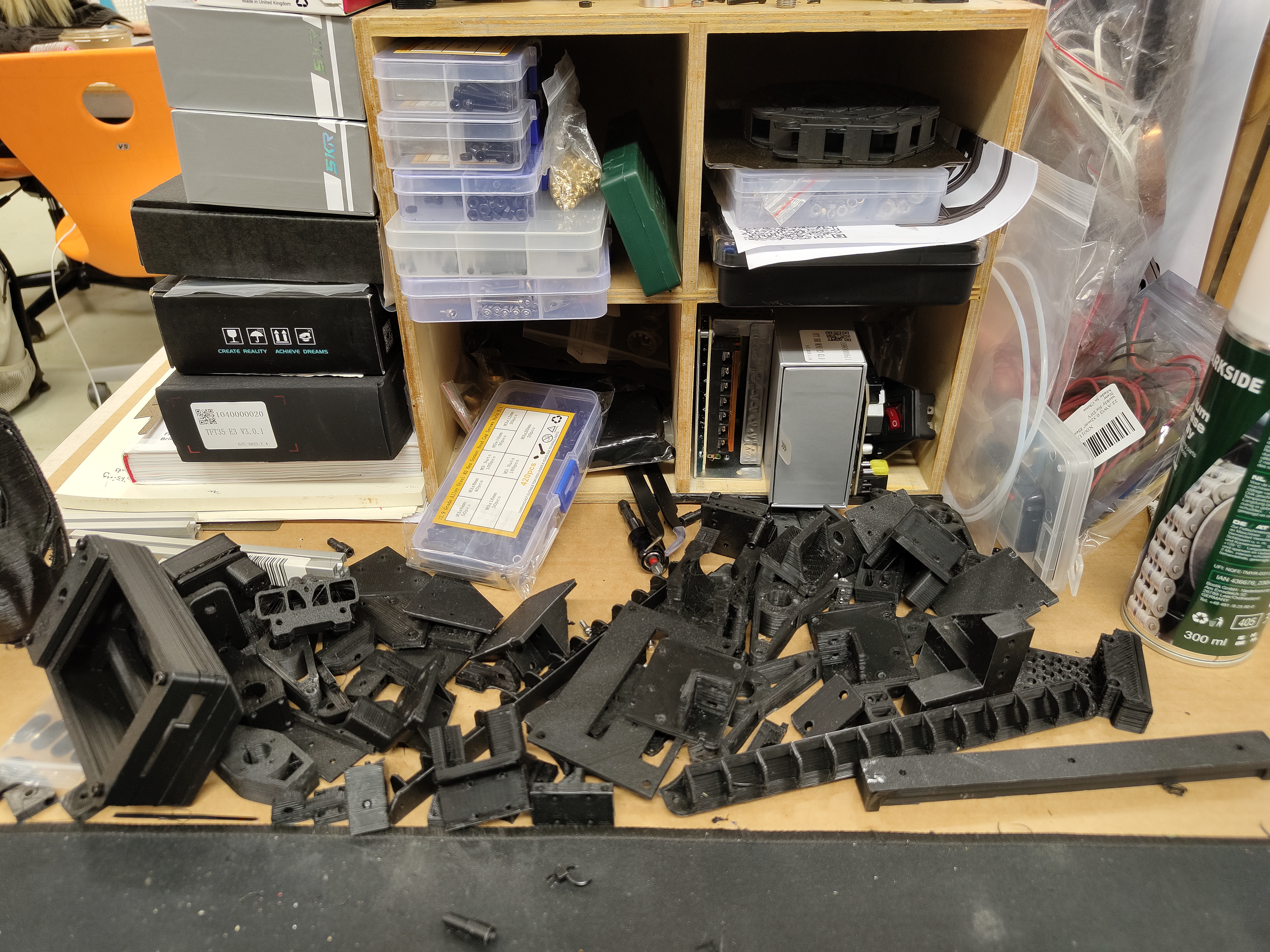
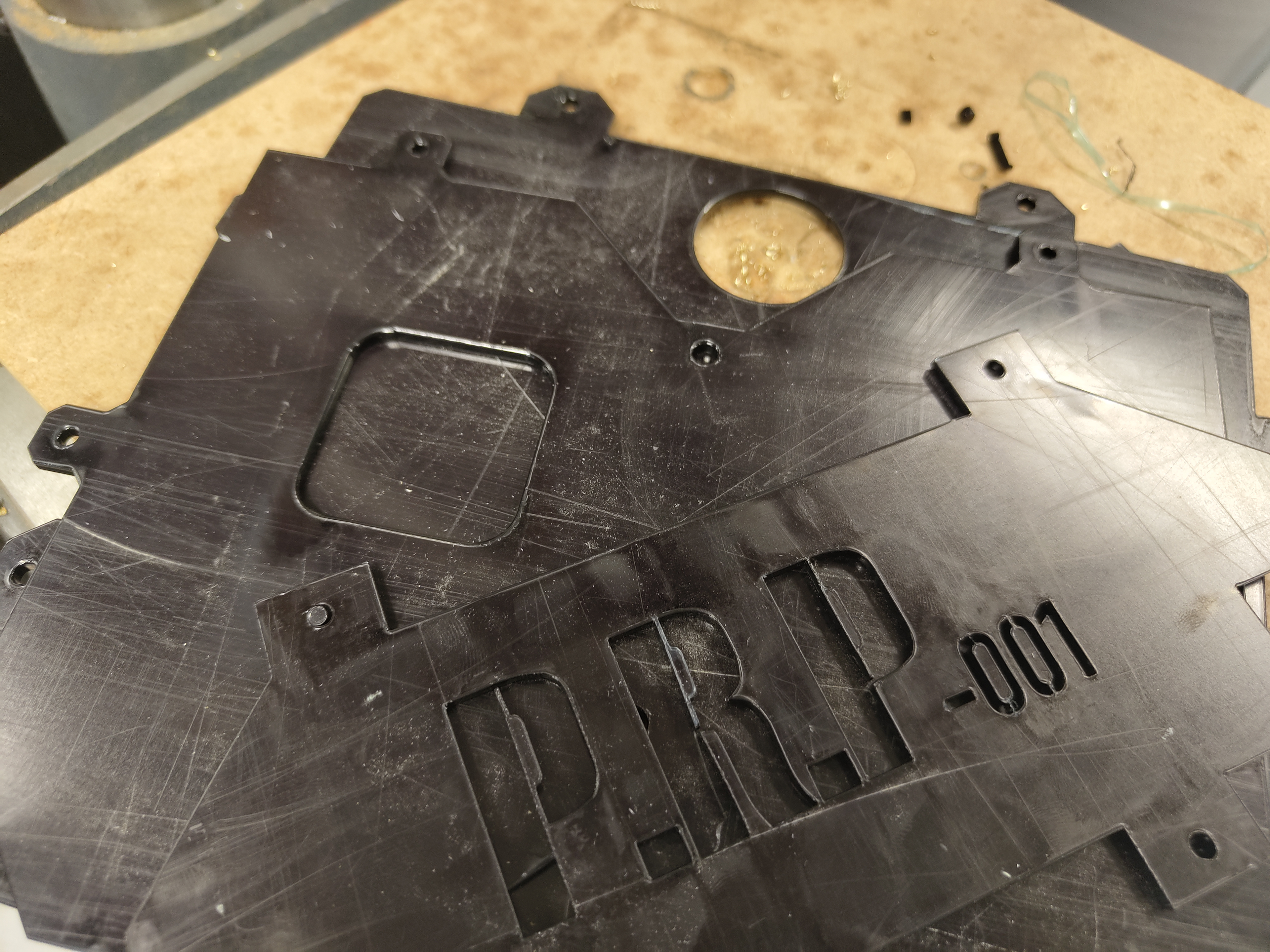
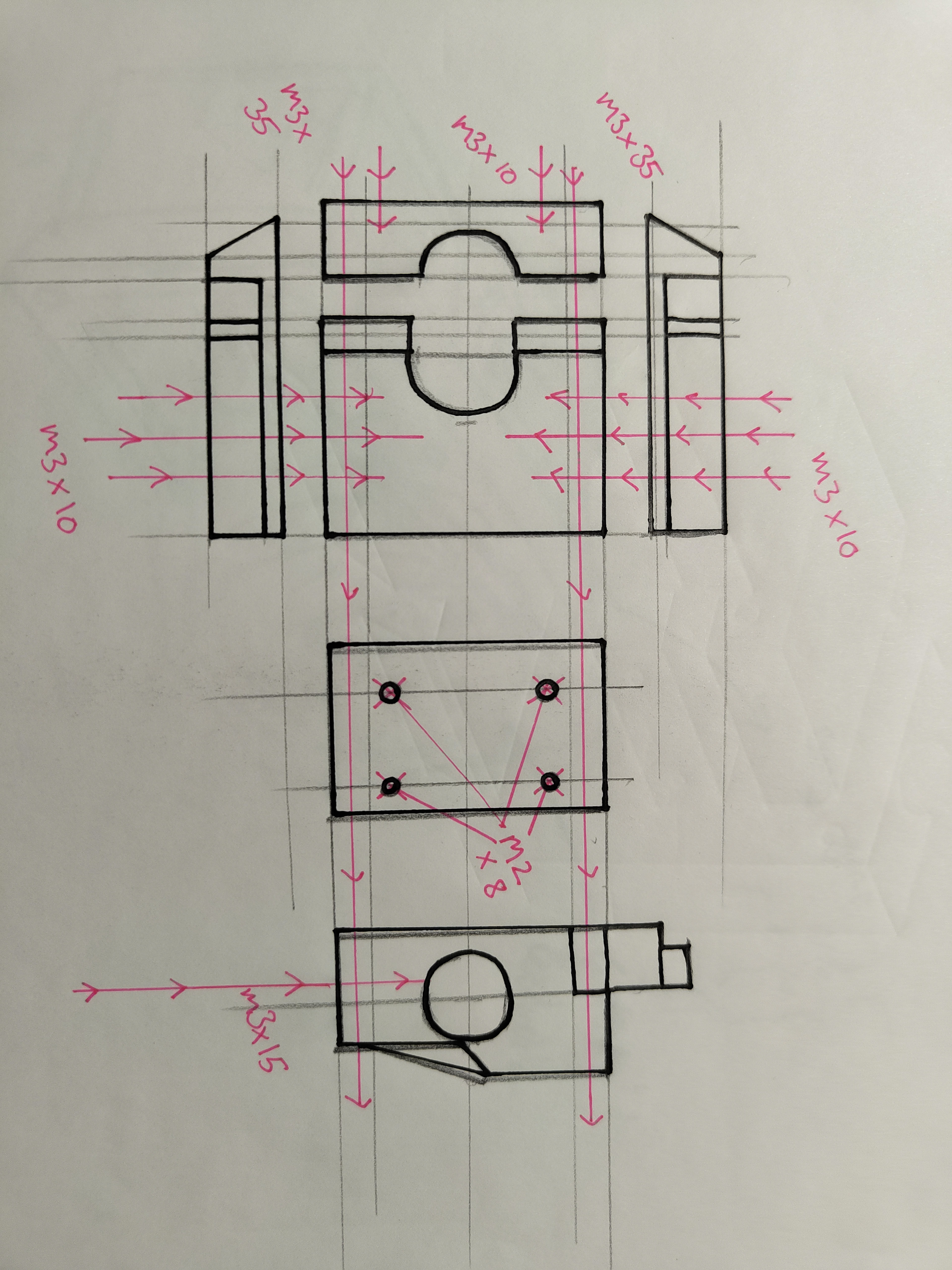
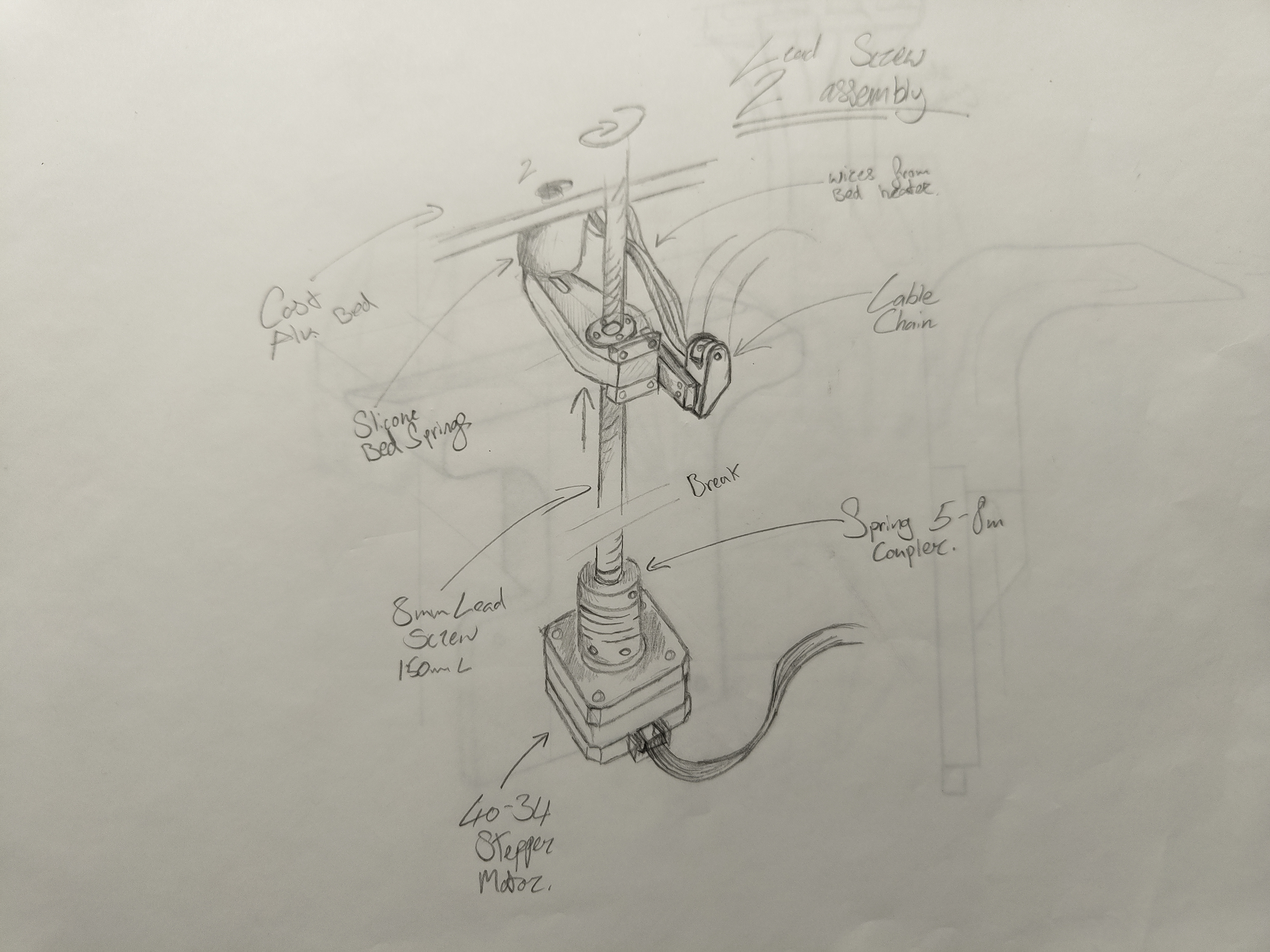
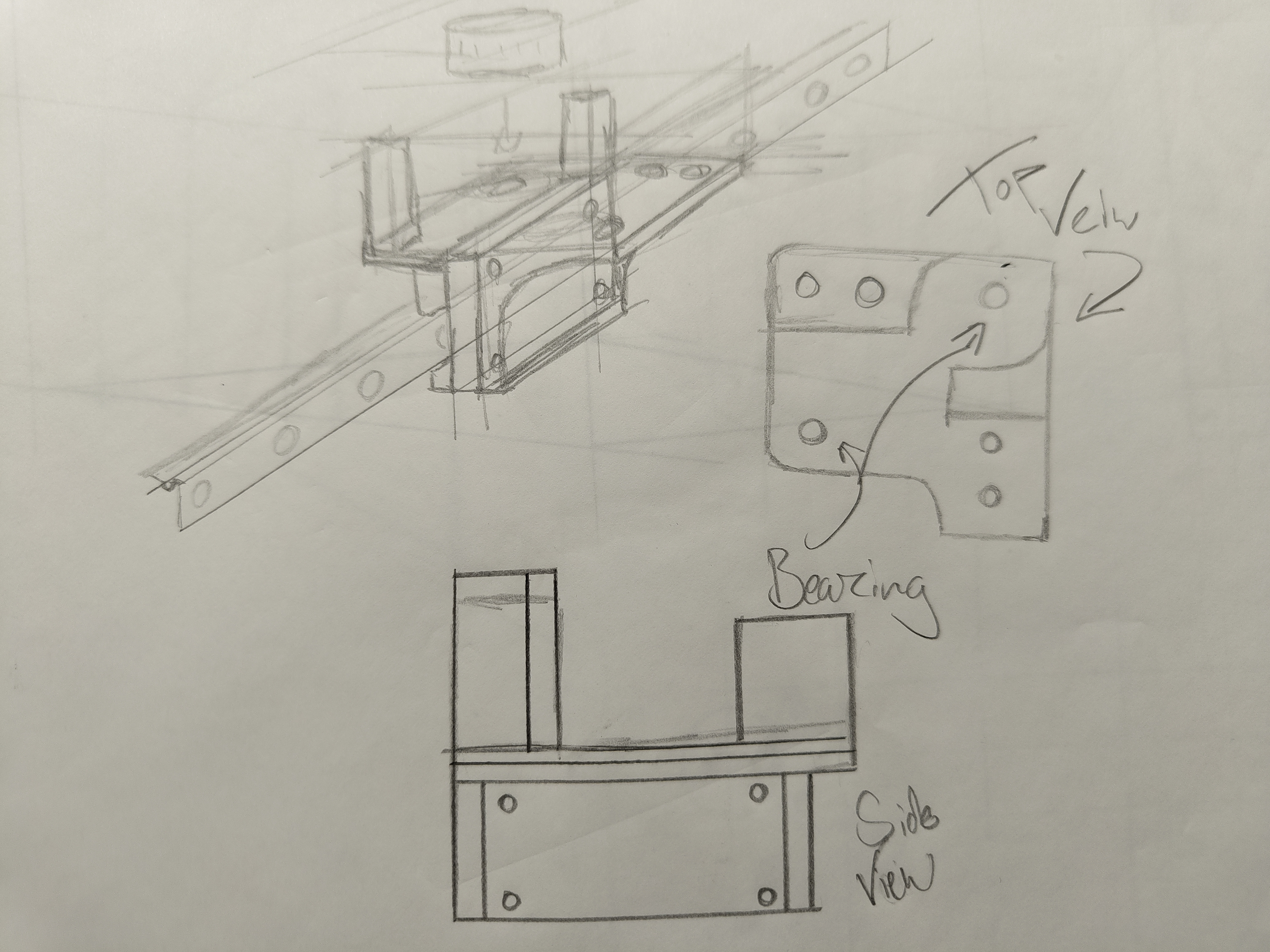
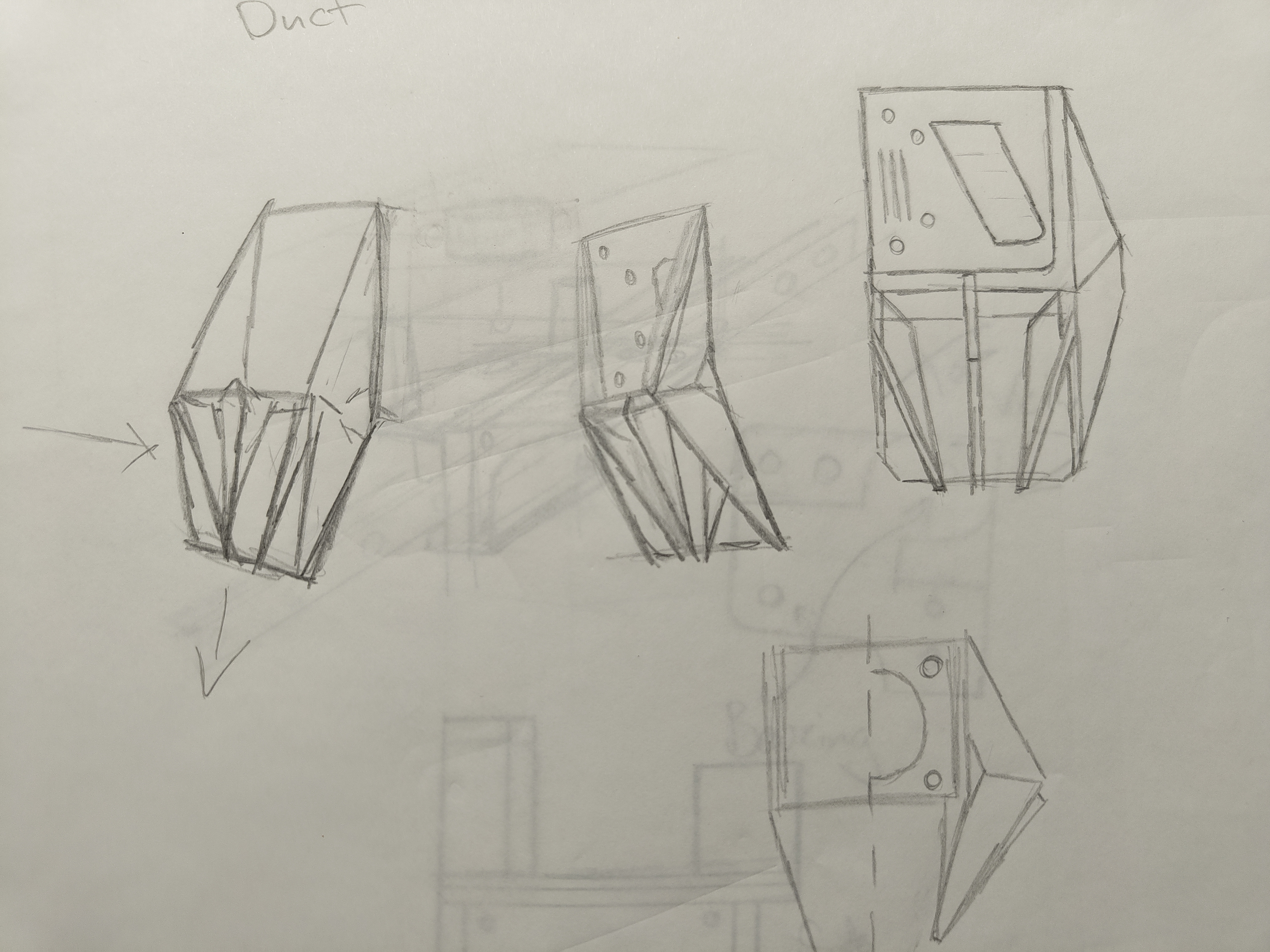
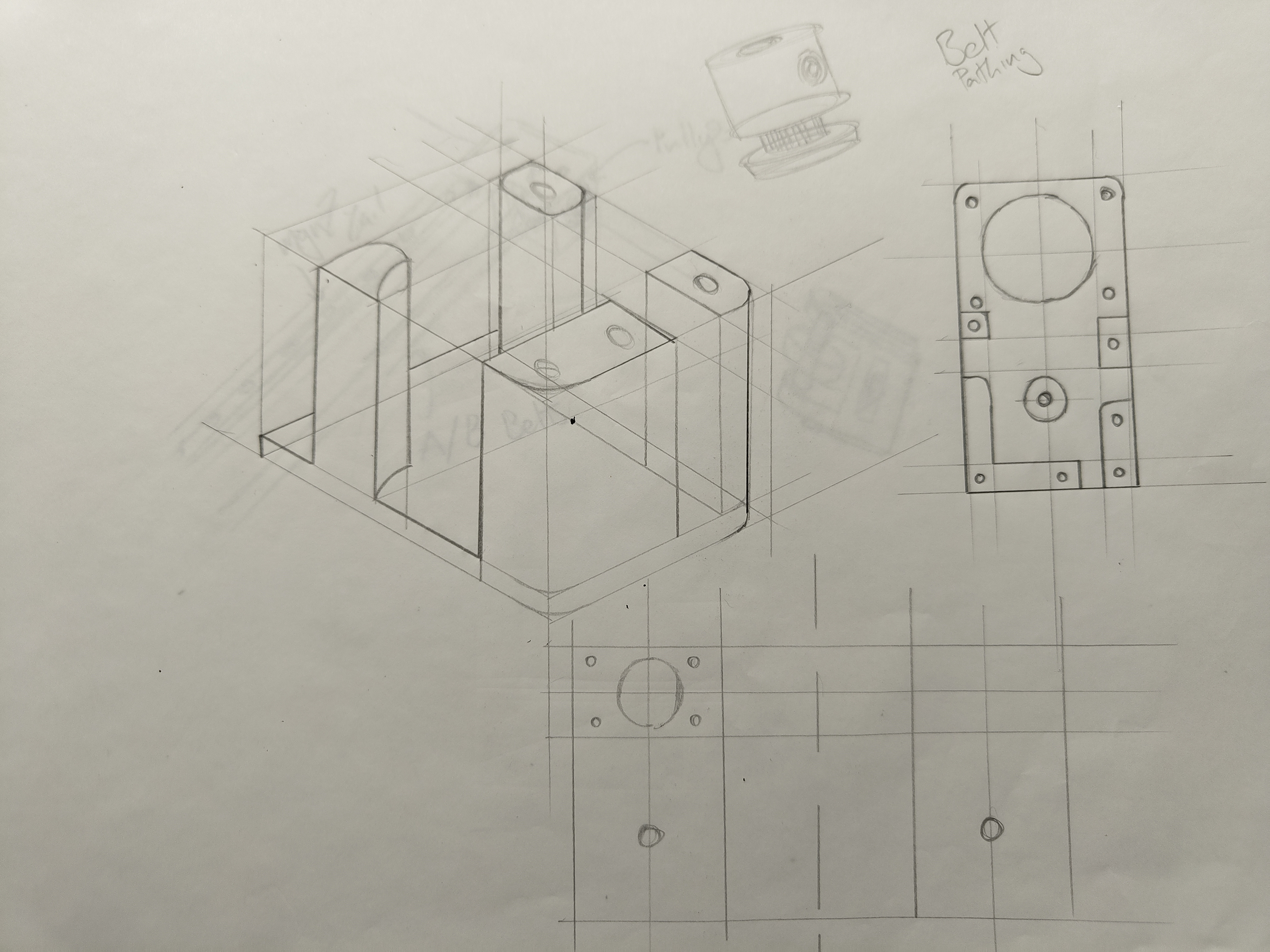
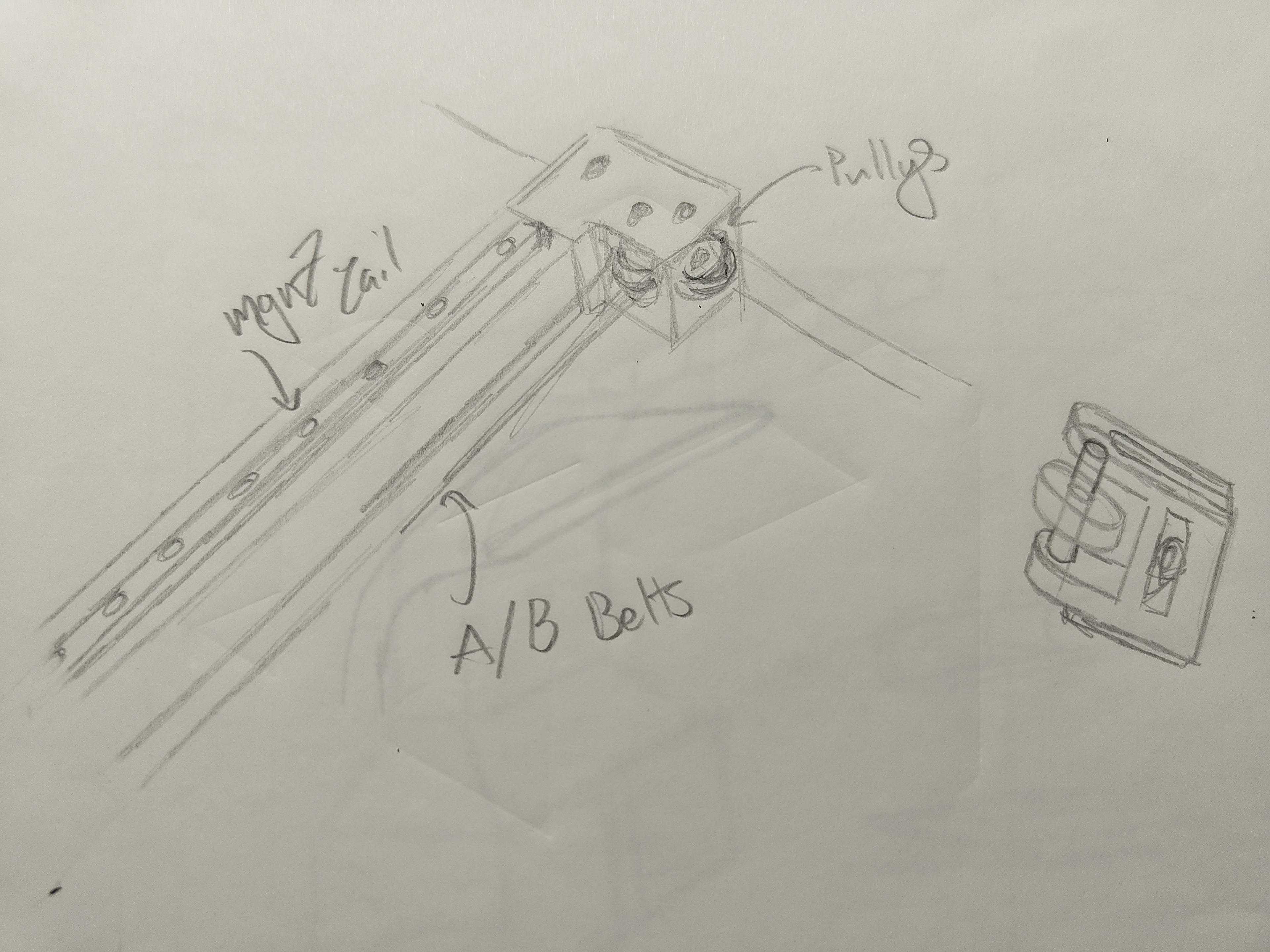
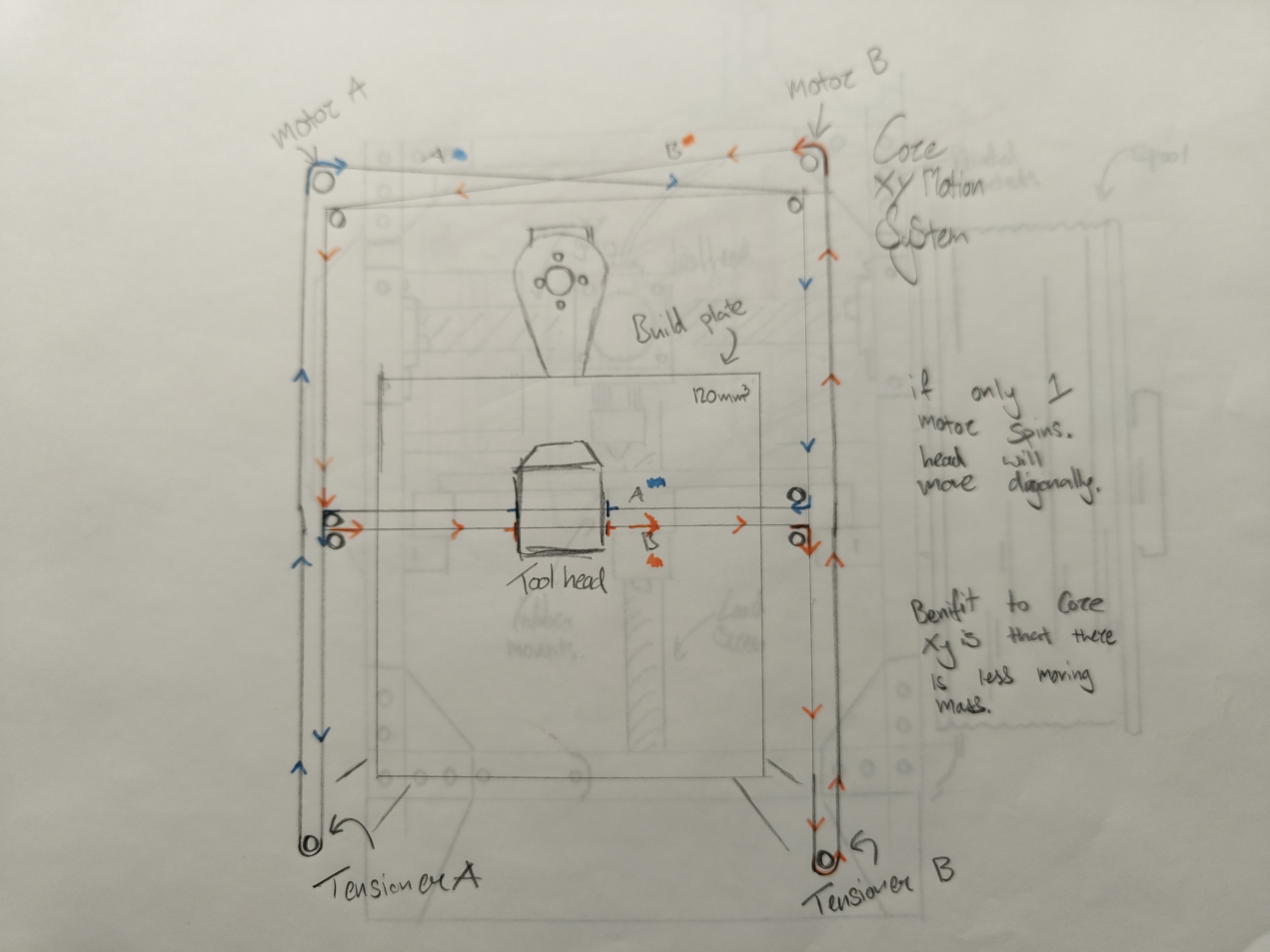
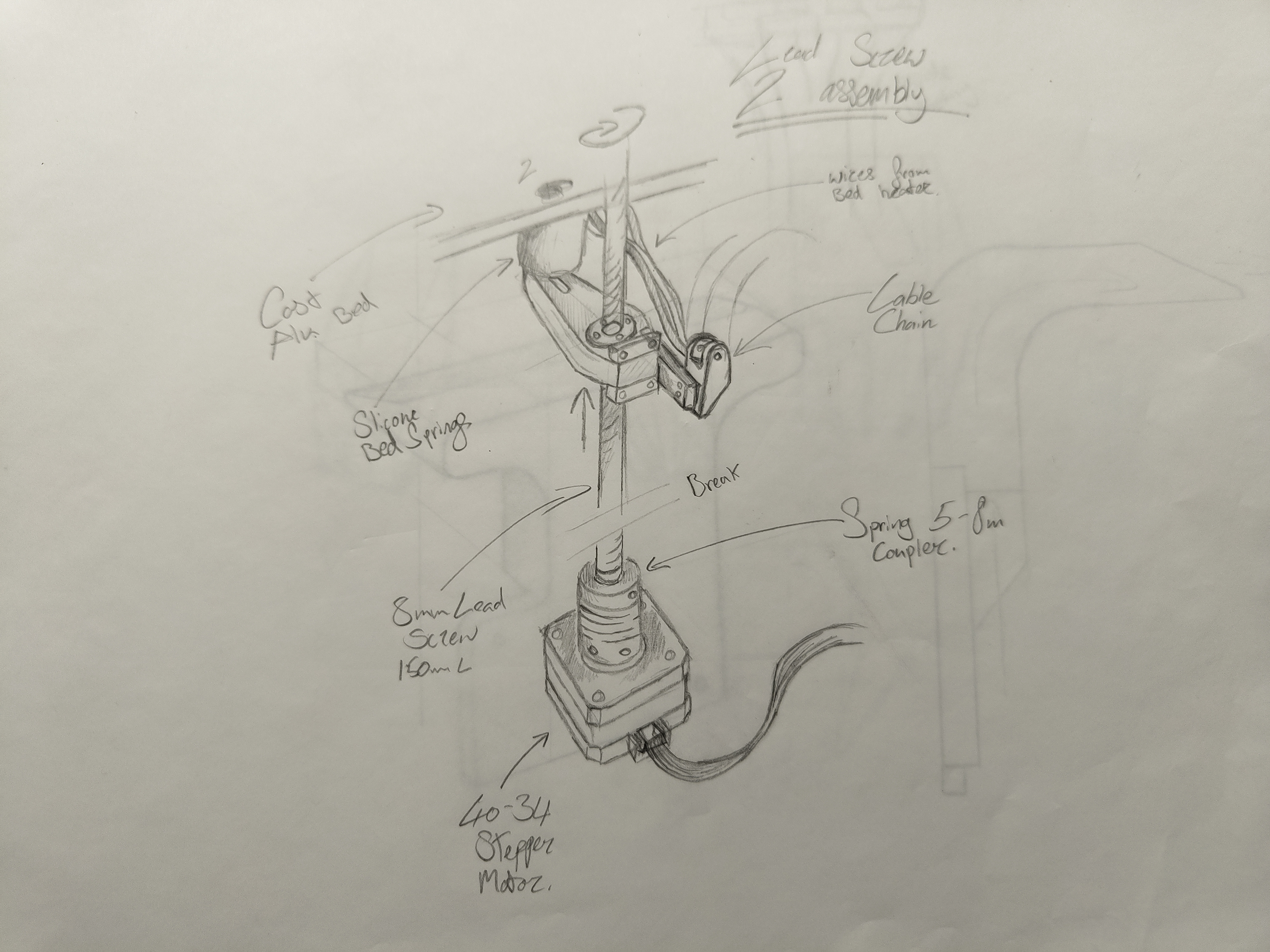
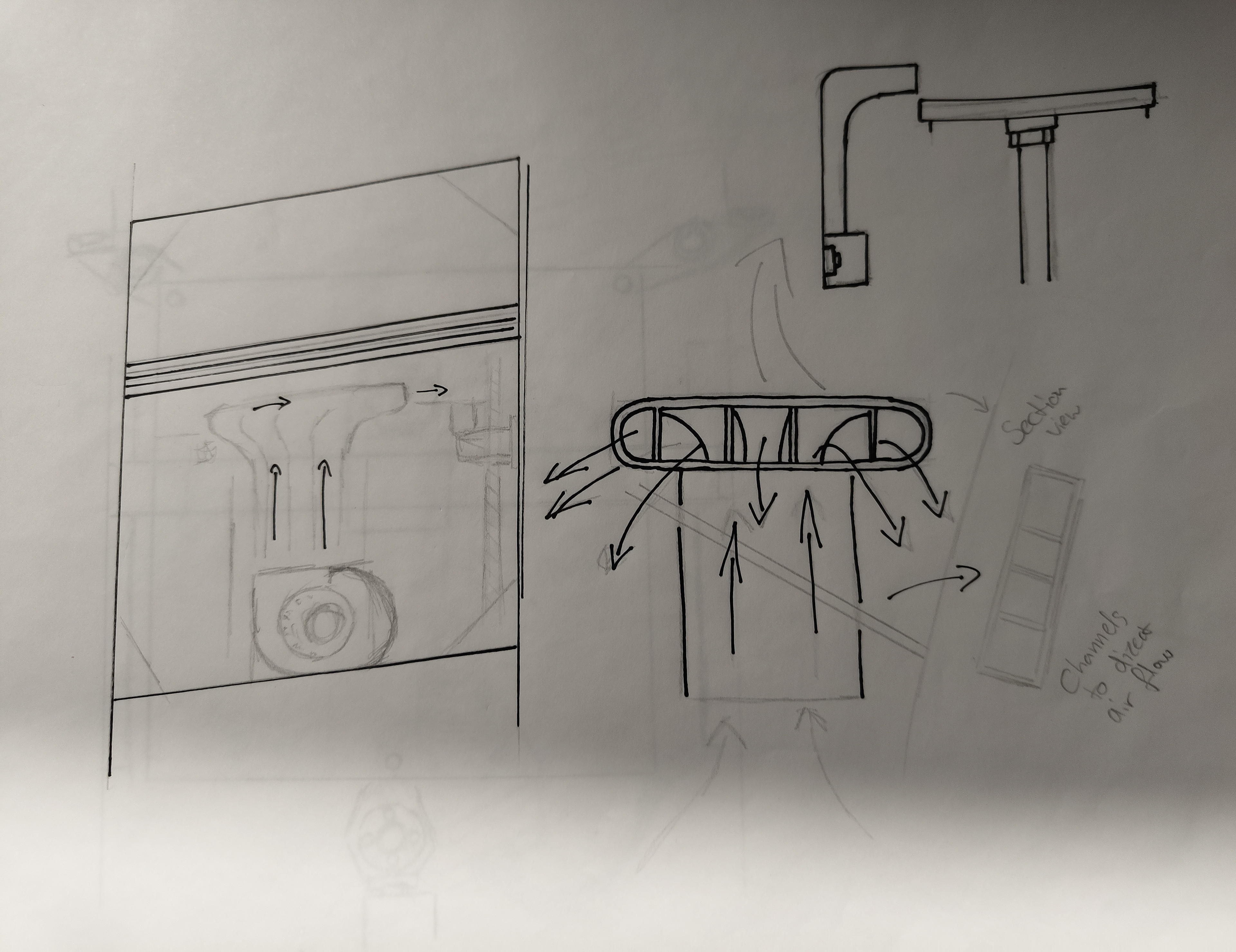
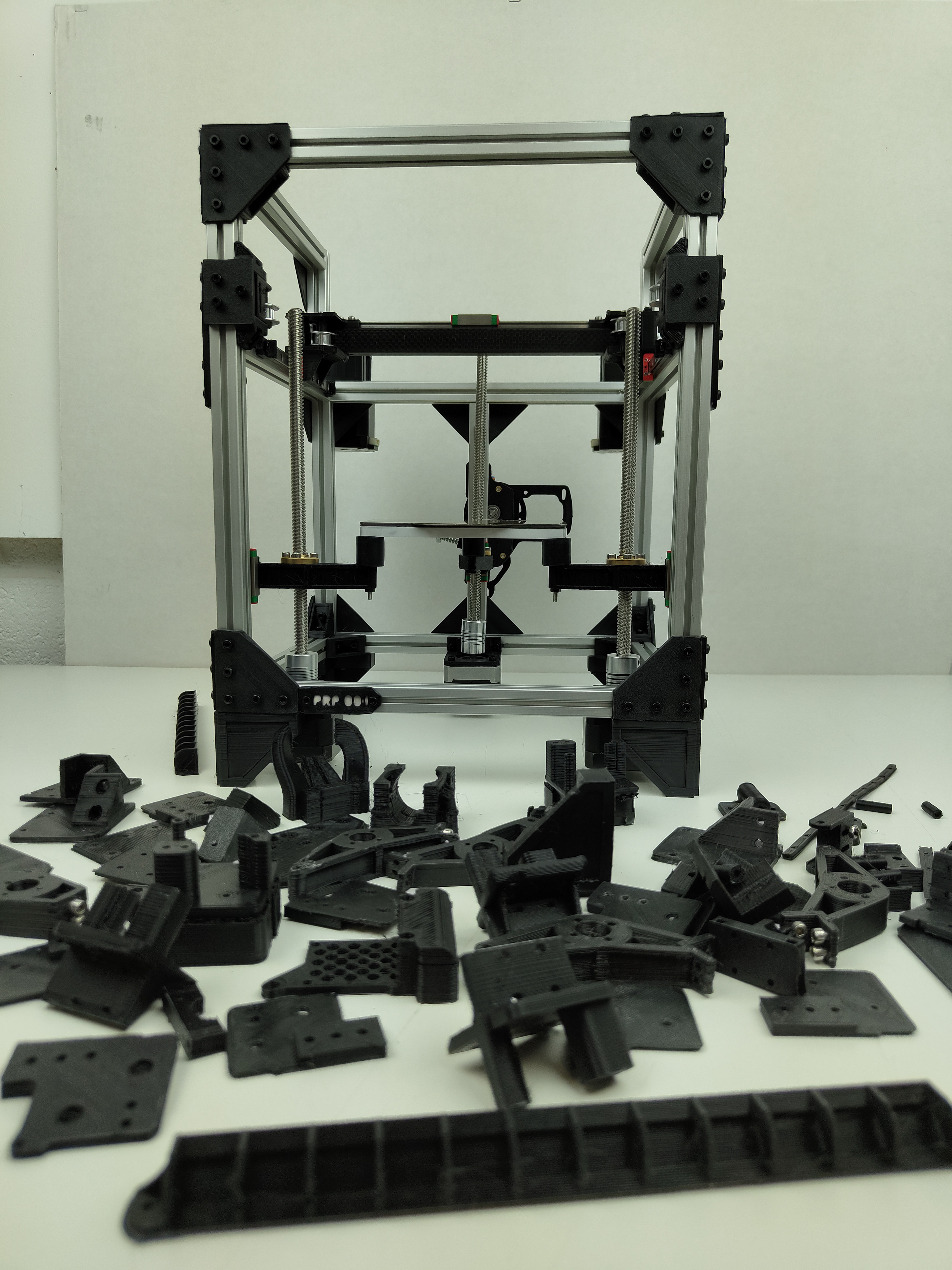
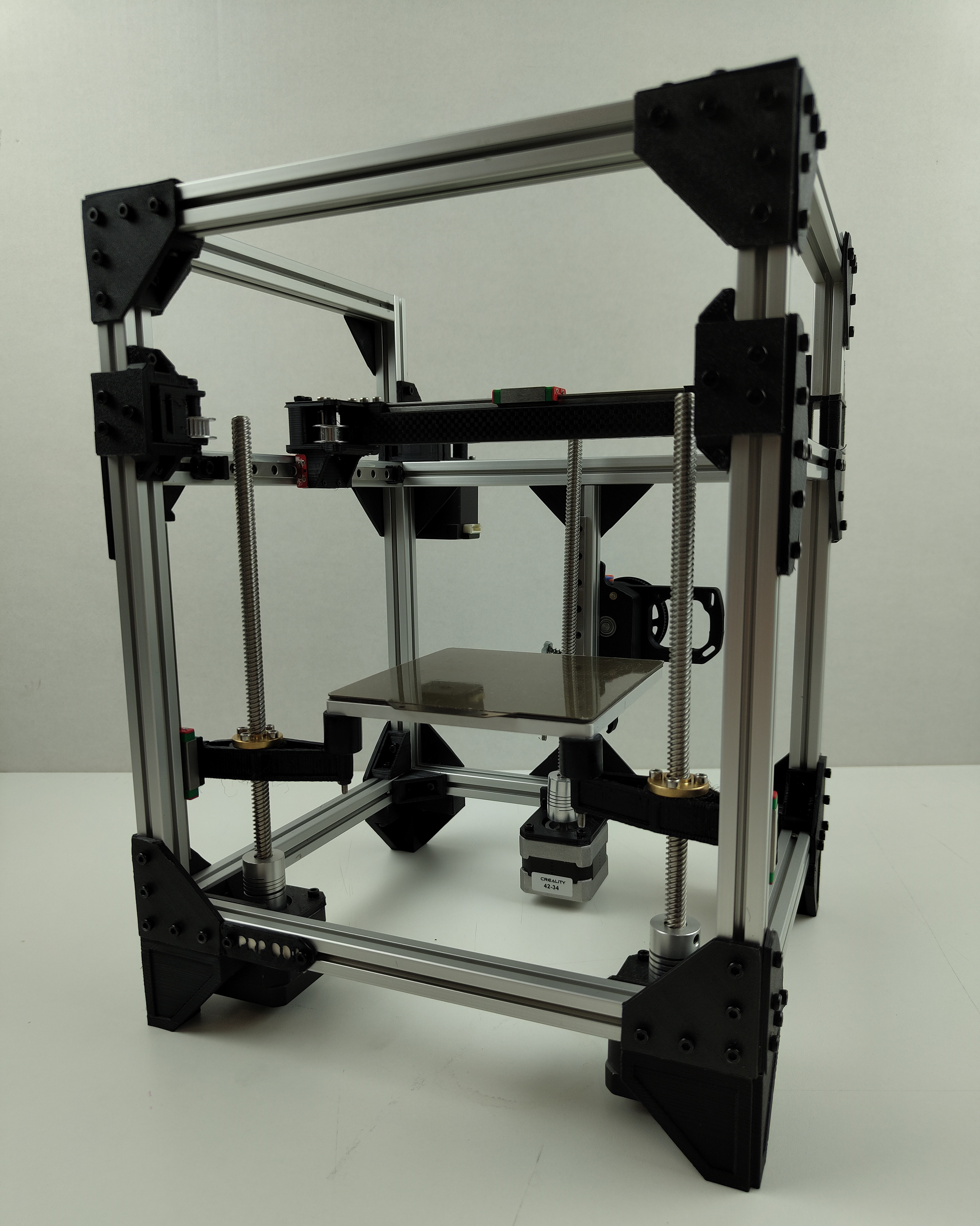
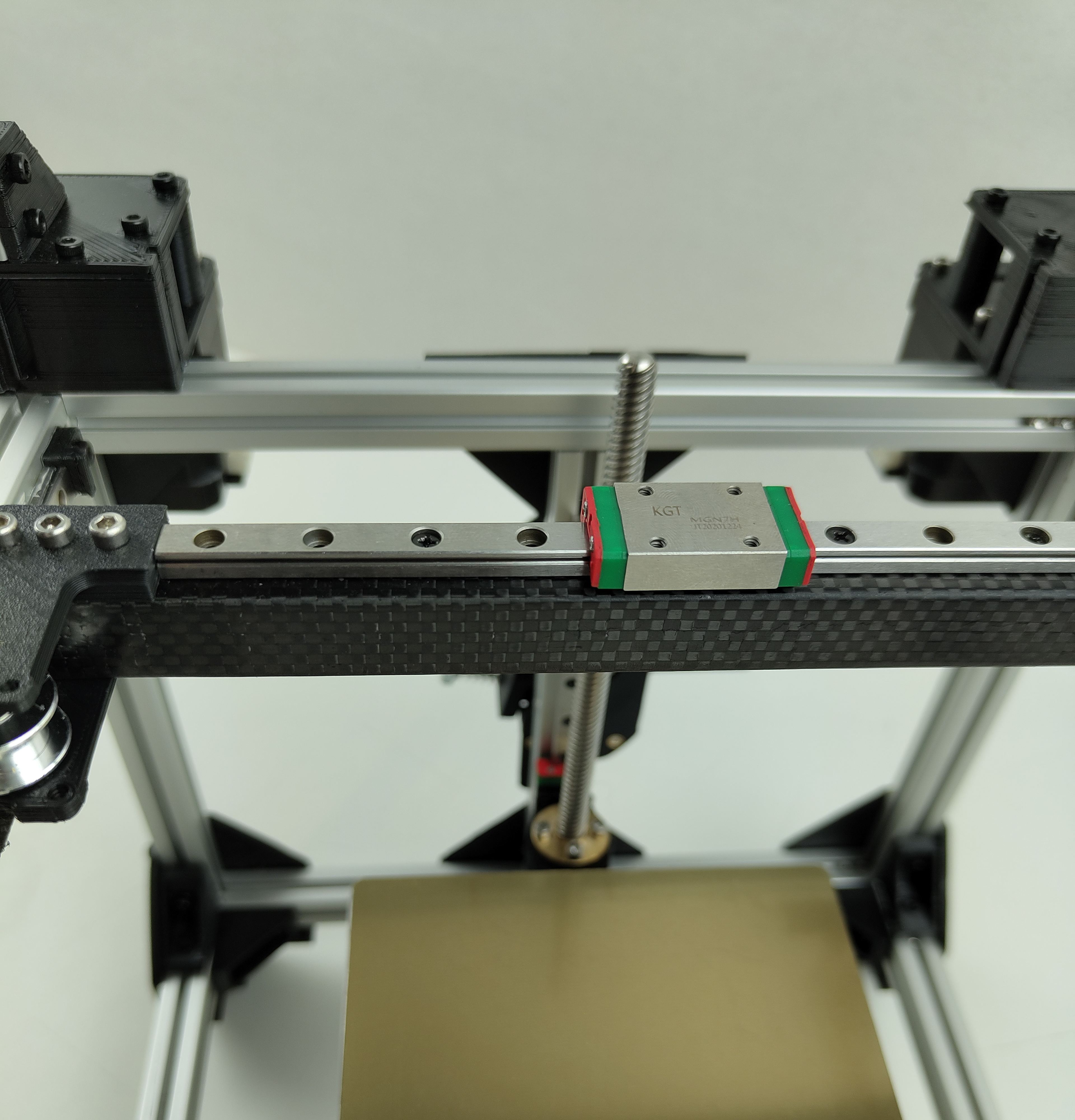
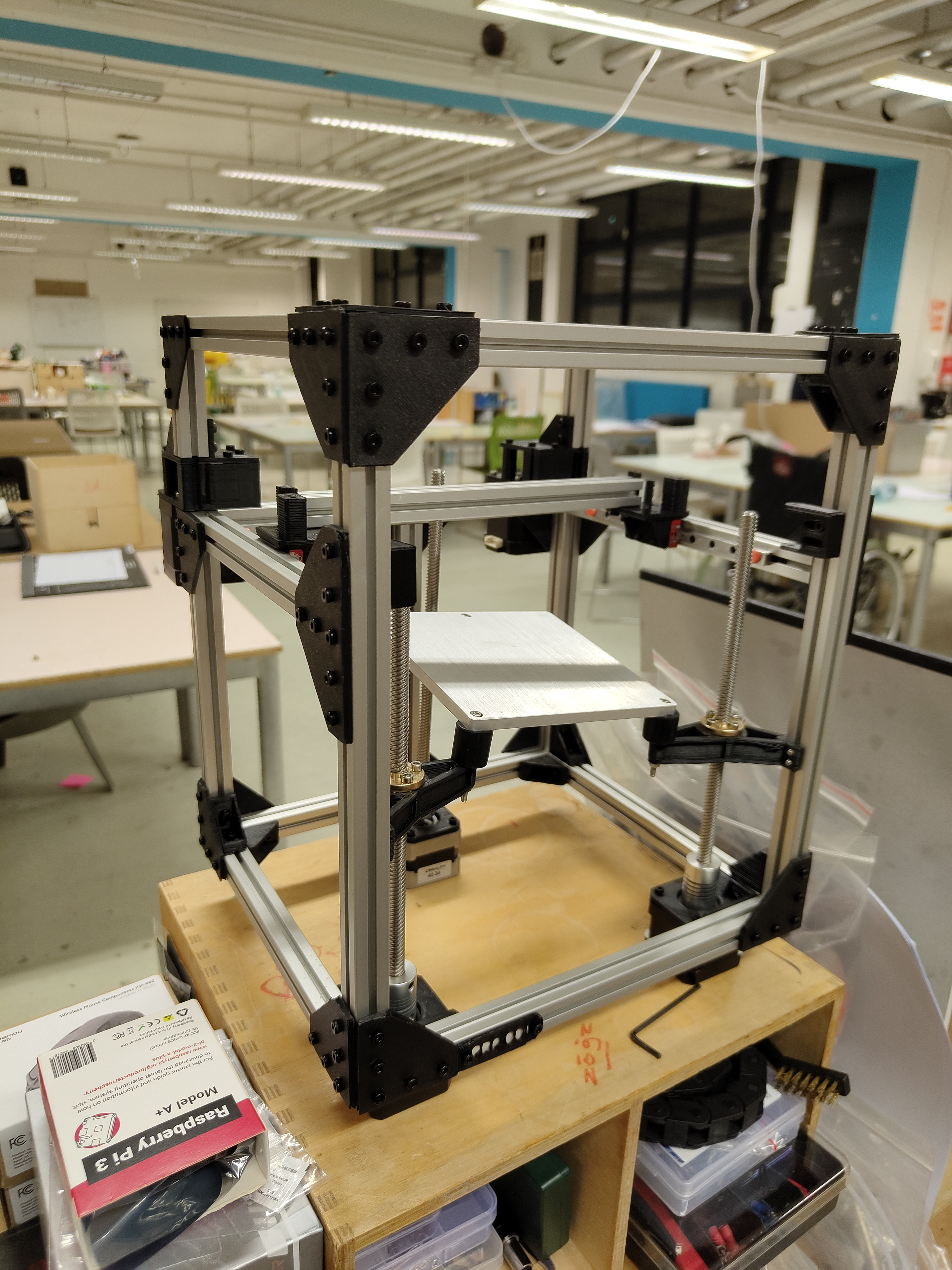
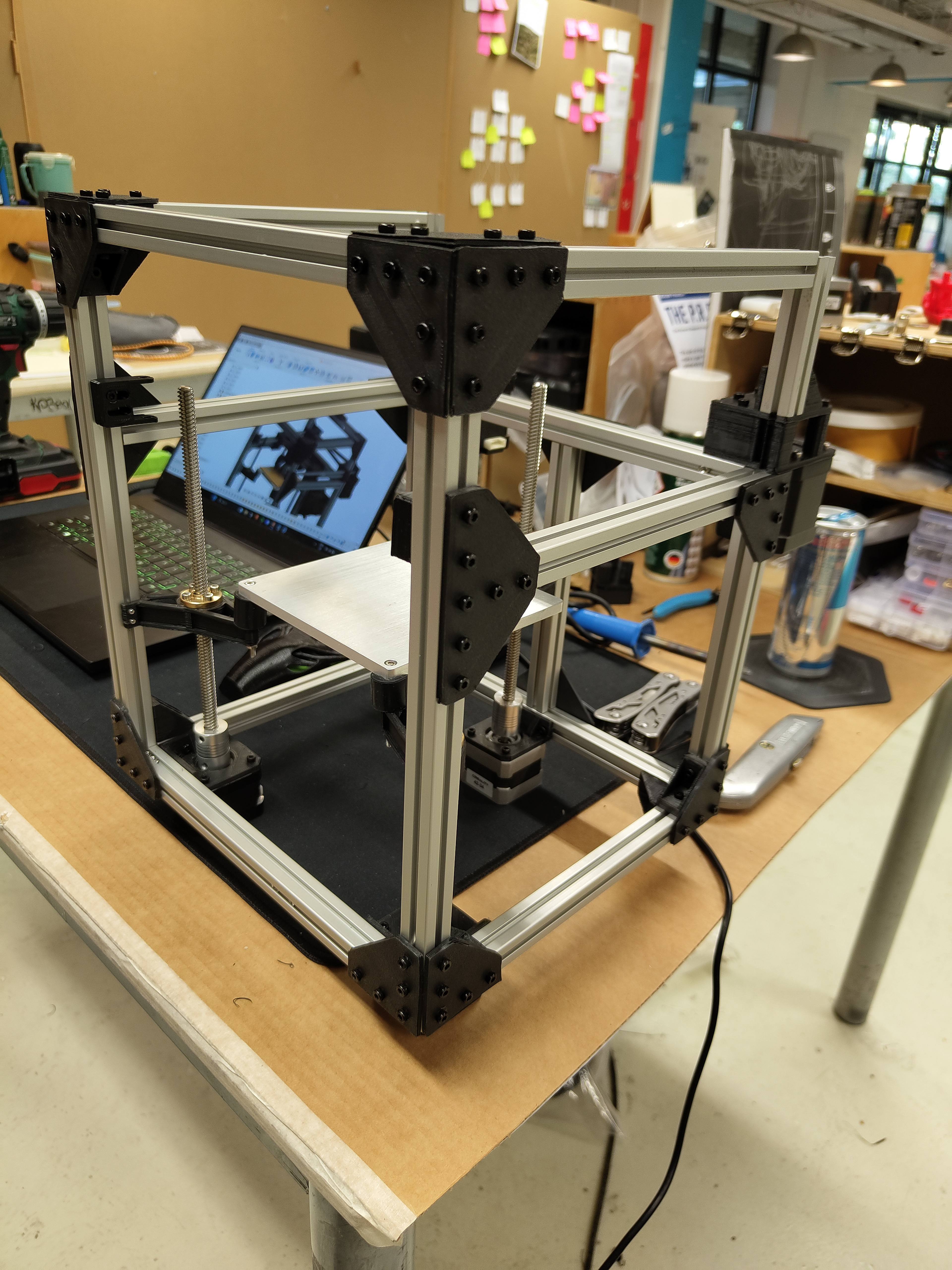
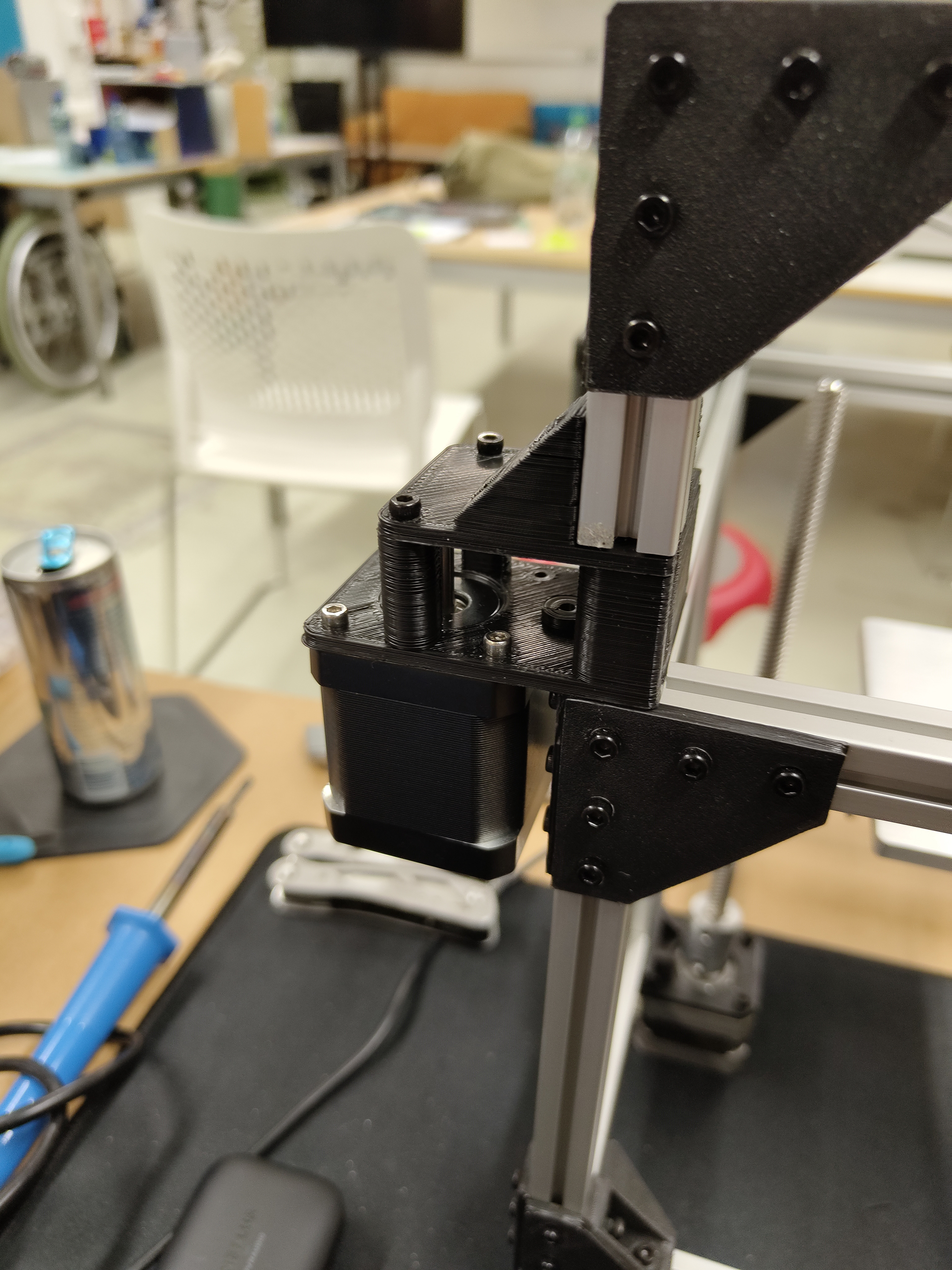
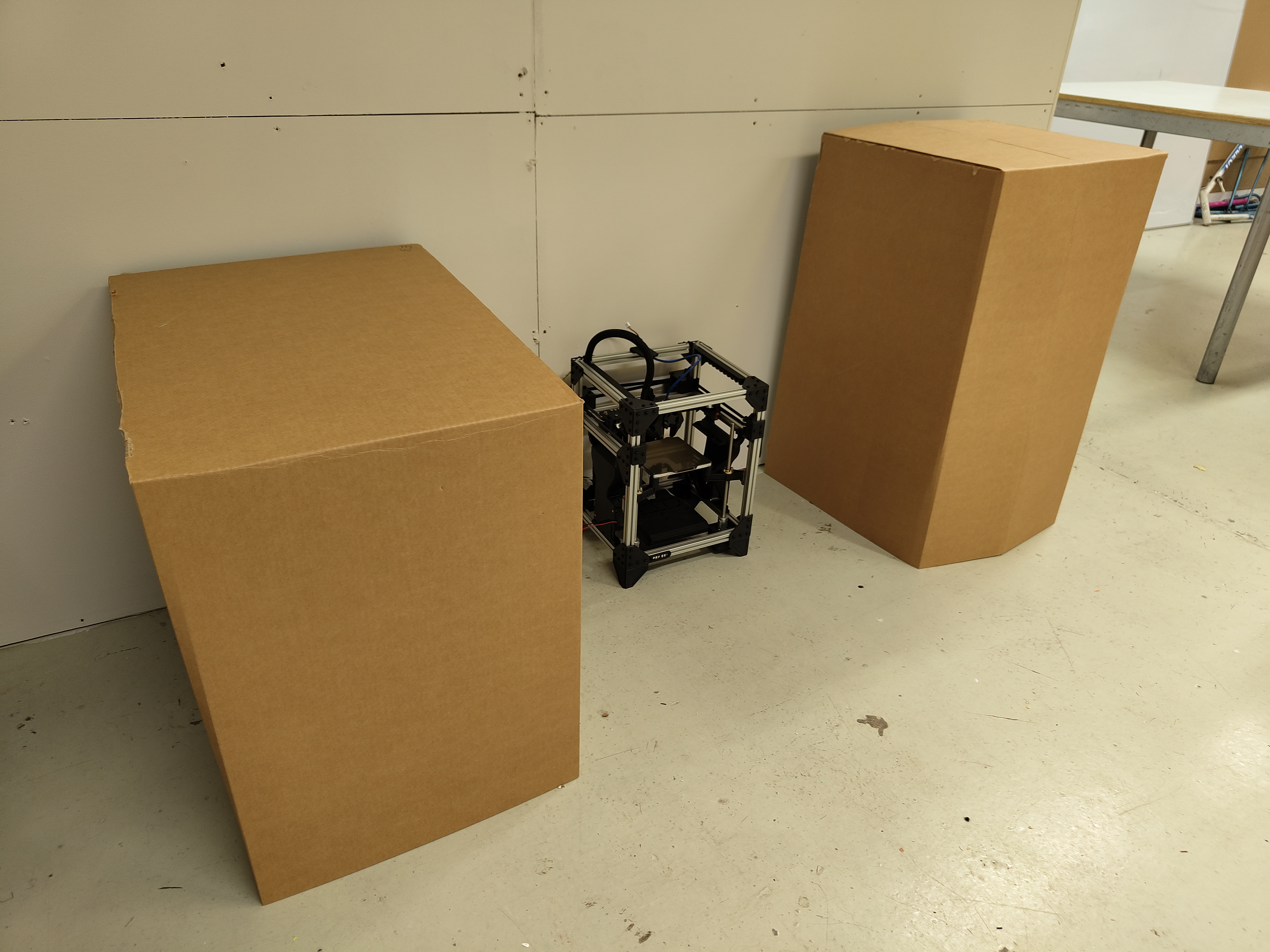
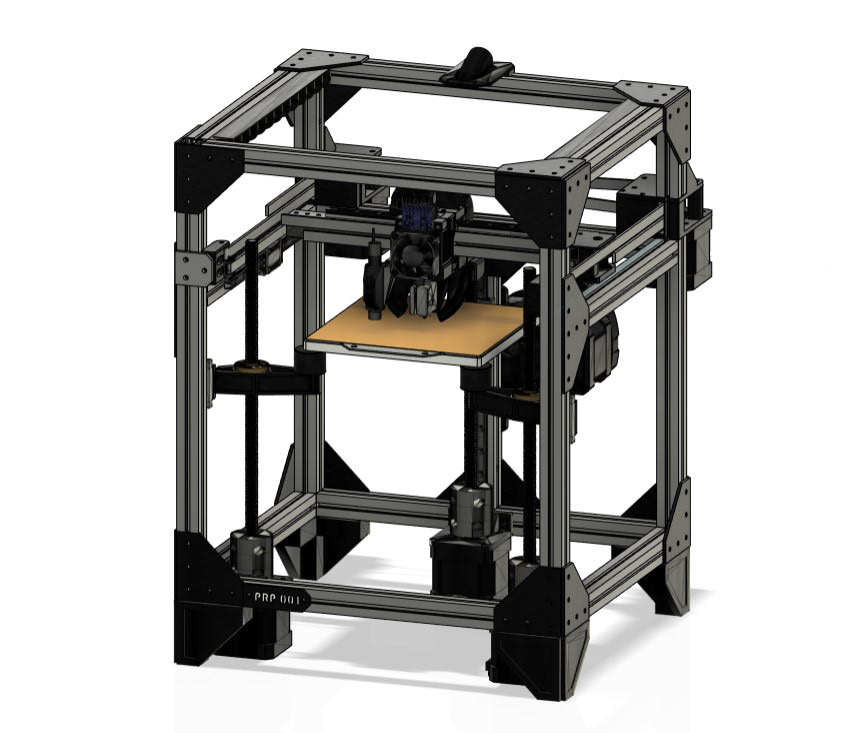
Throughout this phase of the project i used alot of the learnings from modifying my other 2 printers quite extensively, this stage was still quite challenging from an engineering perspective.
Shown to the left are some of the progress images of the first section of the build process, this set the frame work of the project as it dictated alot of the key elements like size, volume, motion style, etc.
The "P.R.P-001" is a 120mm cubed, corexy, Klipper ran printer.
This allows features like...
- self diagnostics
-High speed printing with imput shaping
-A web interface
-many more.
My heavily modified ender 5 plus (has been overhauled since) which was used to print all the parts for this project.
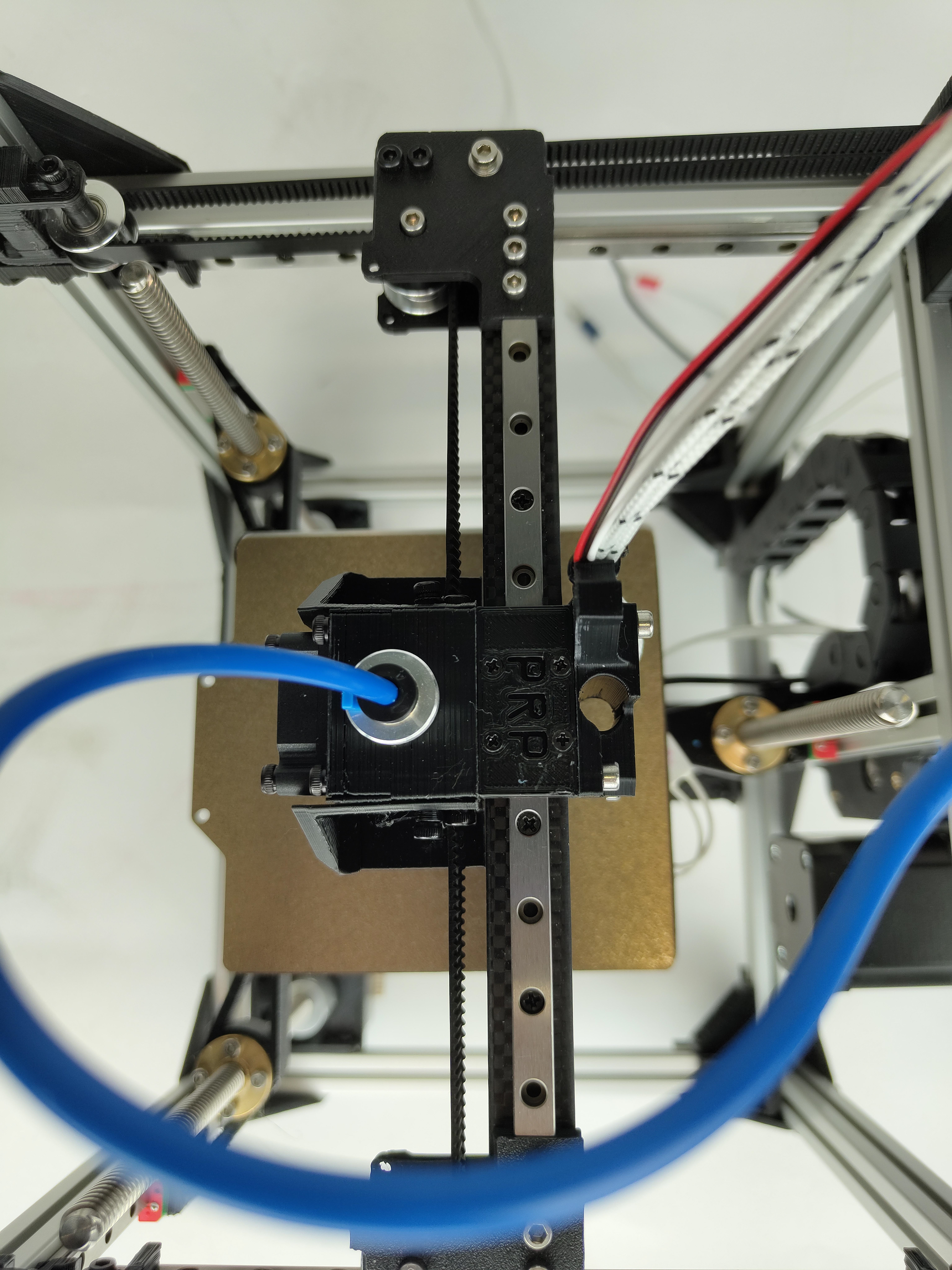
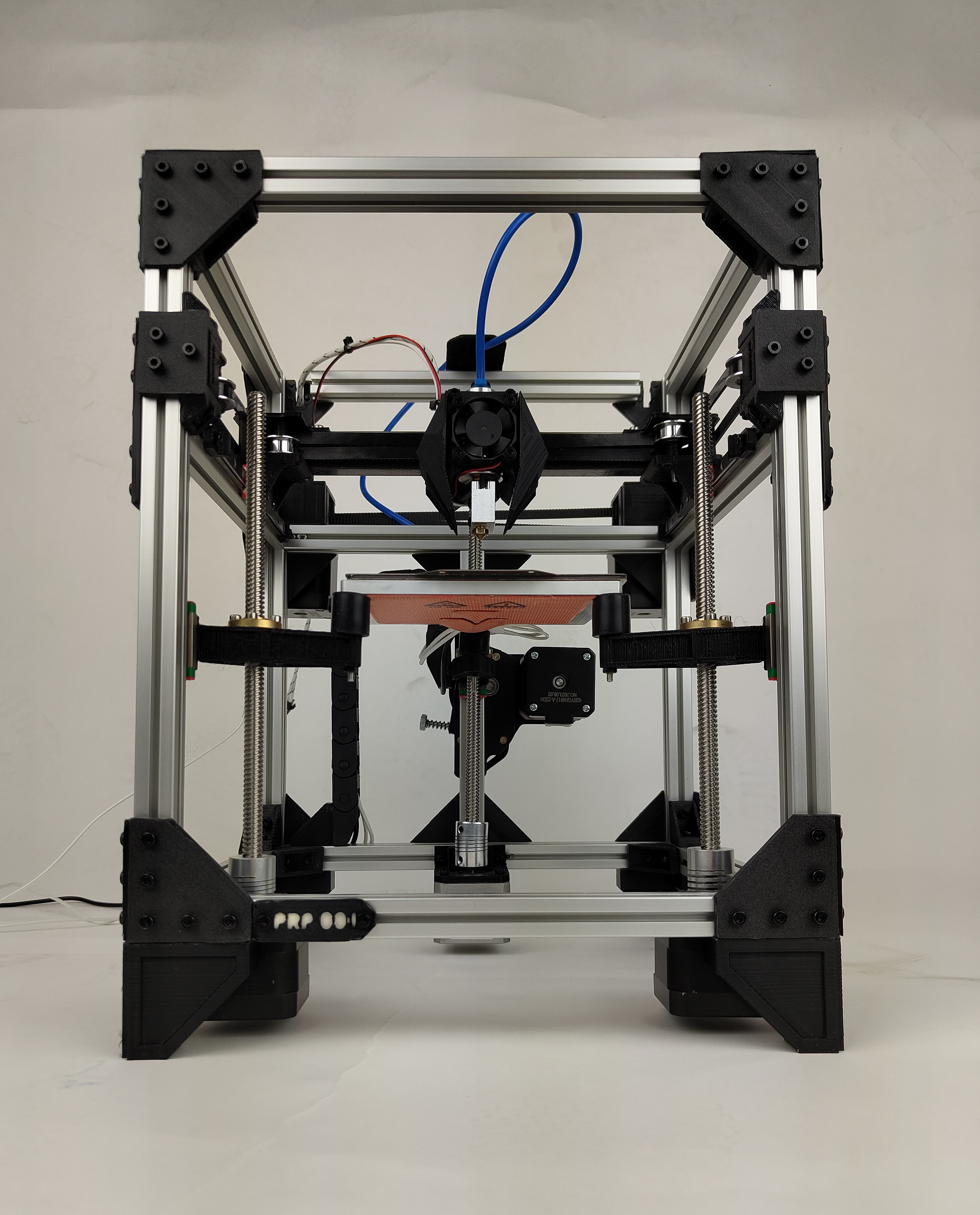
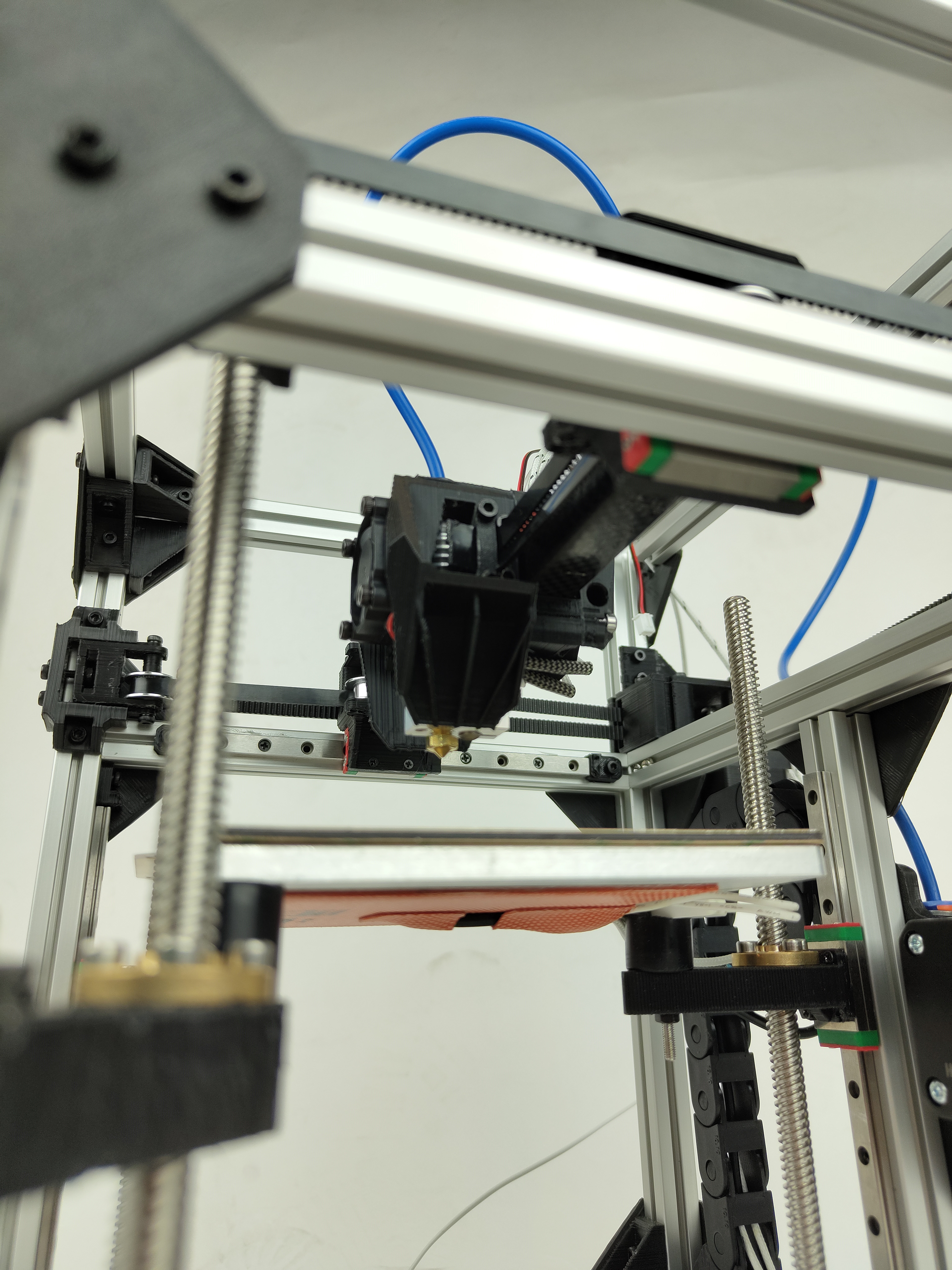
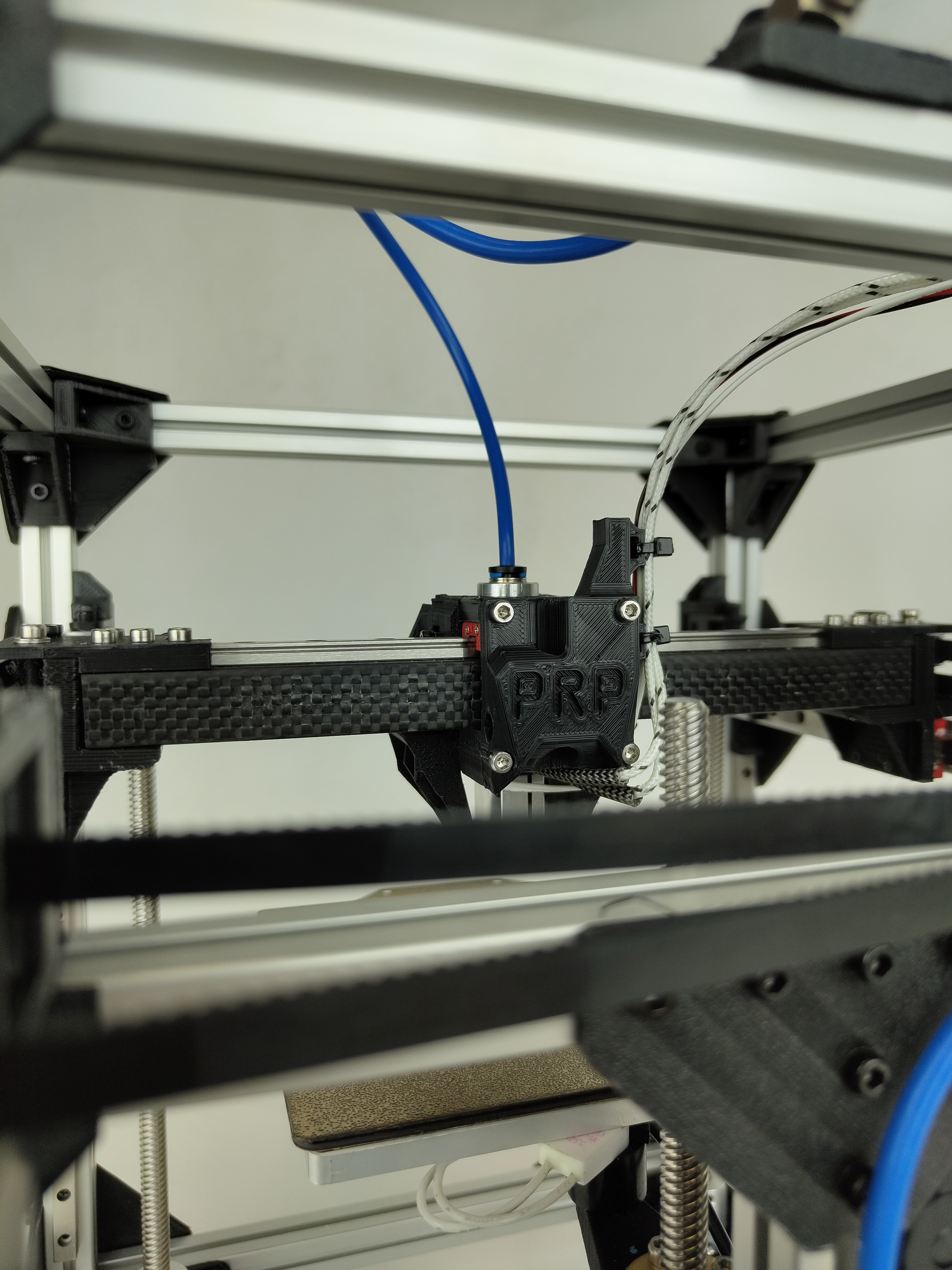
At this point the printer was a functioning motion system without electronics.
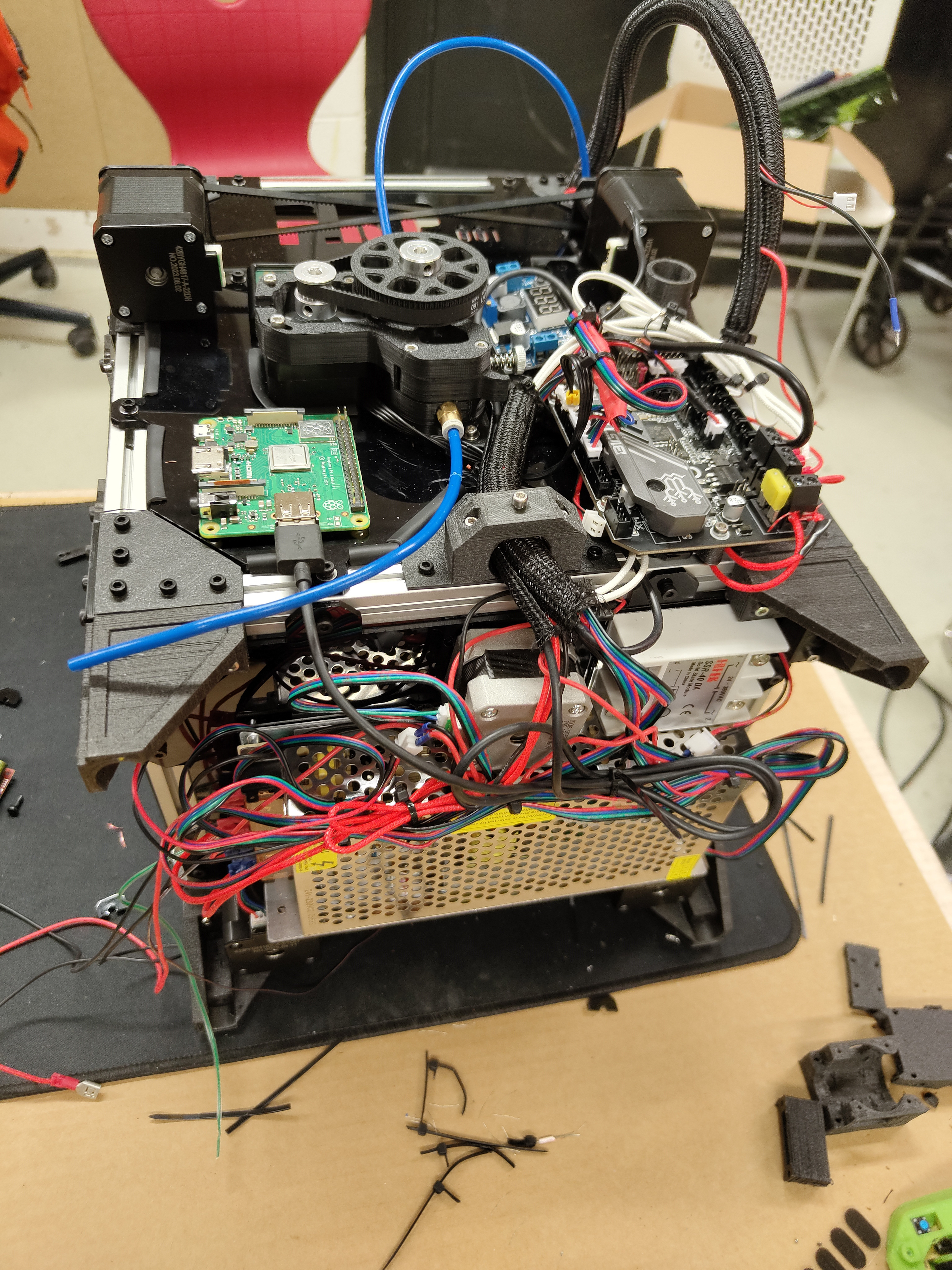
my unorganised wiring
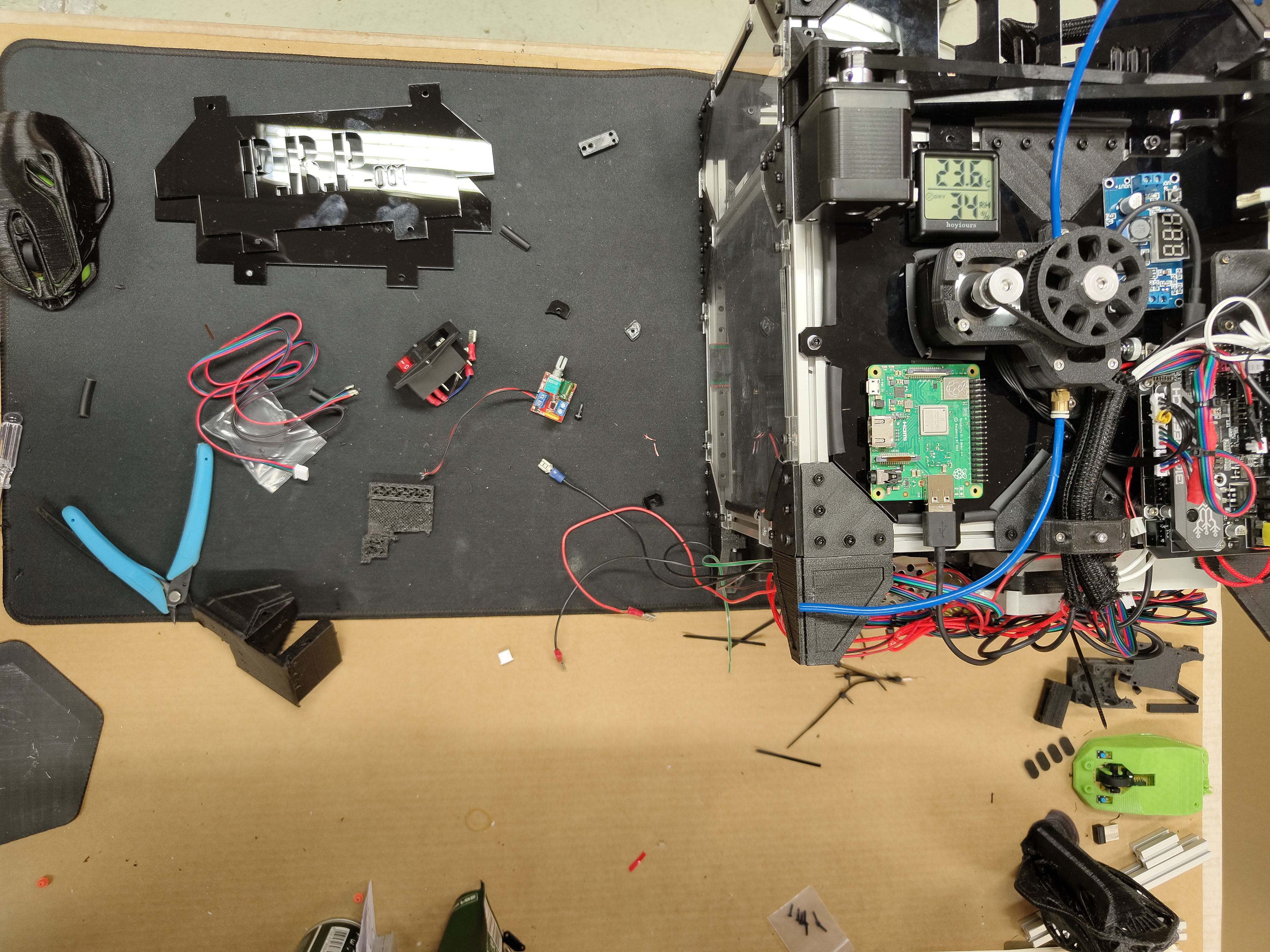
a top down view of my desk
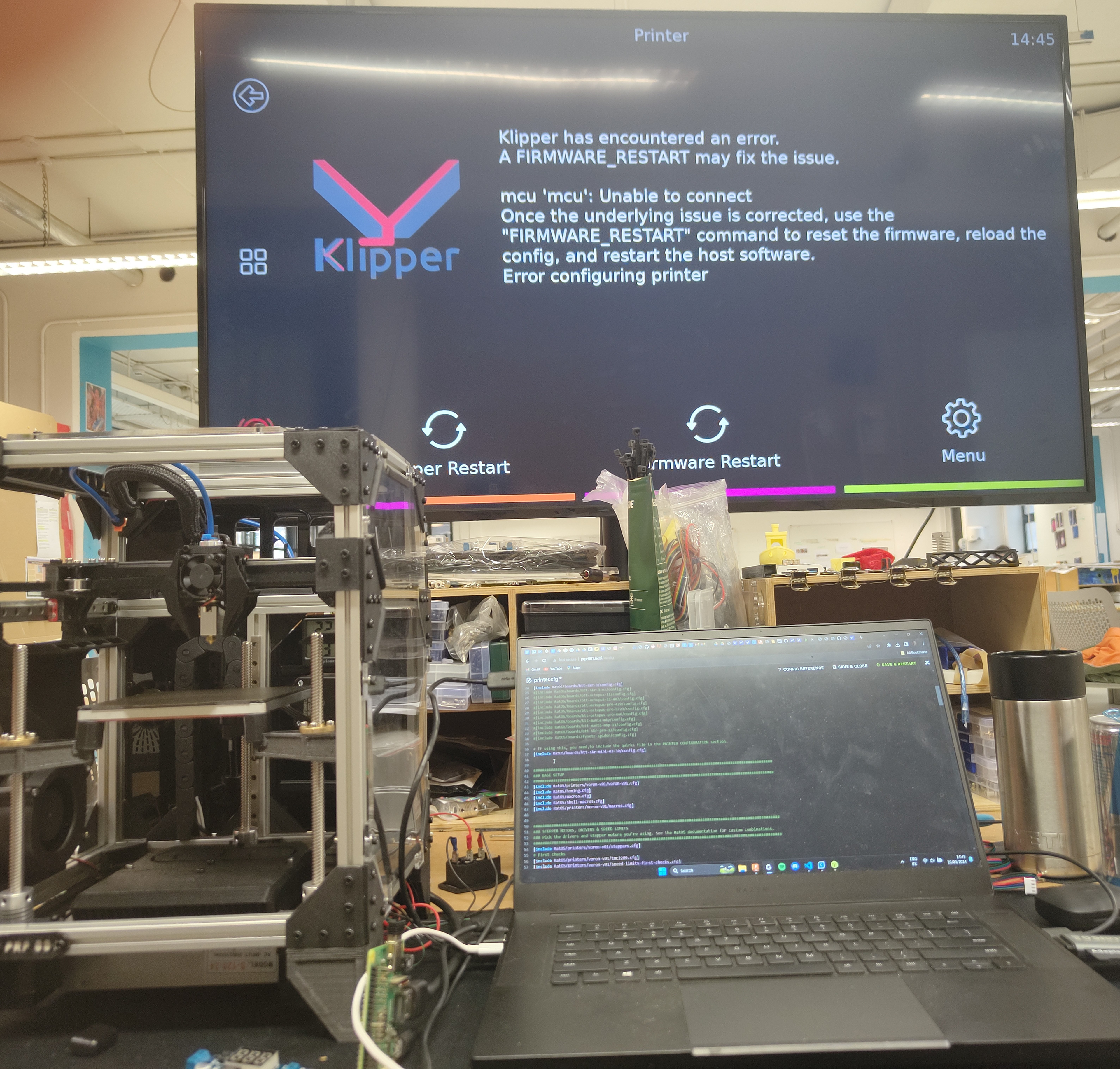
My first attempt at getting klipper running
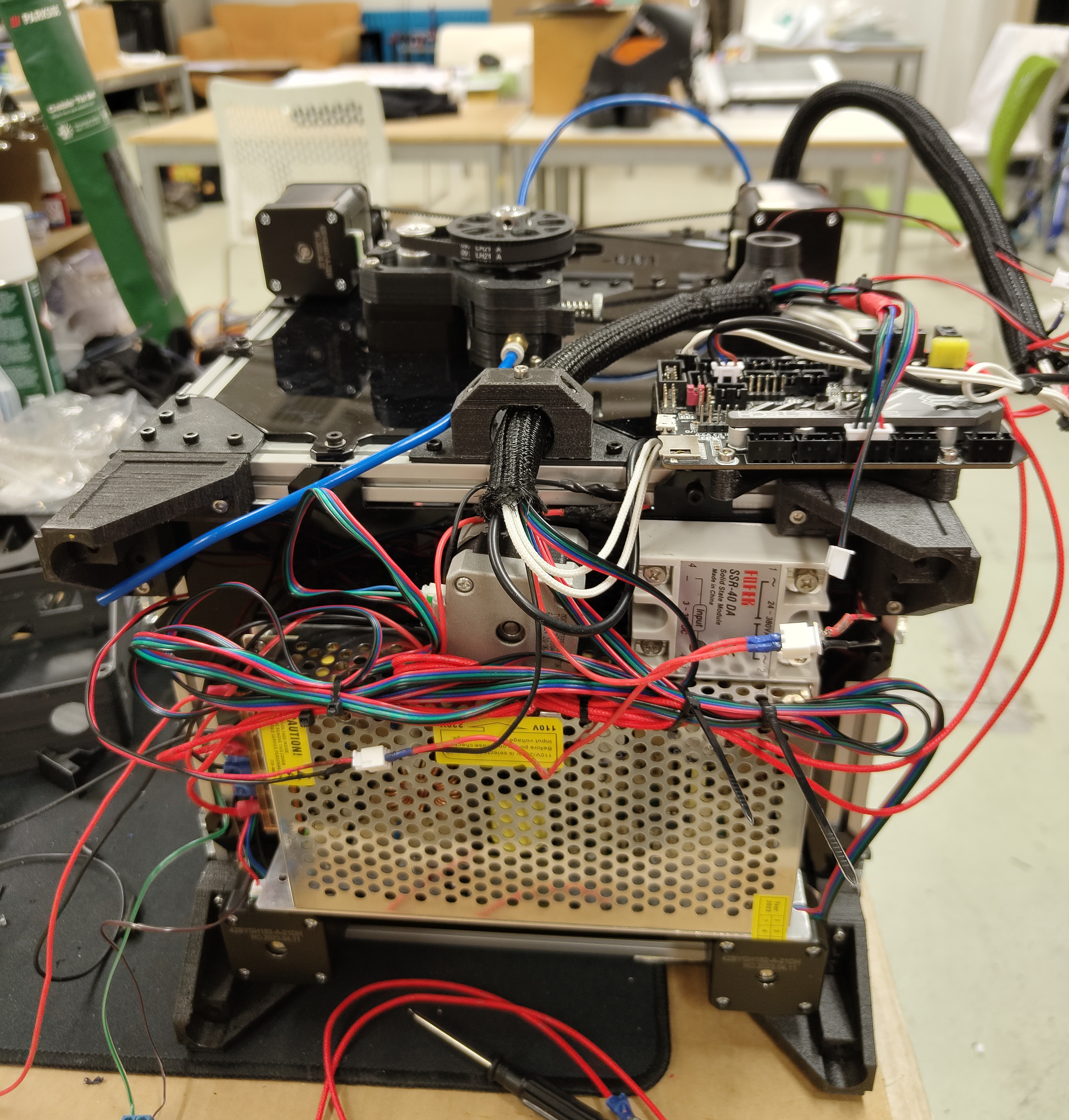
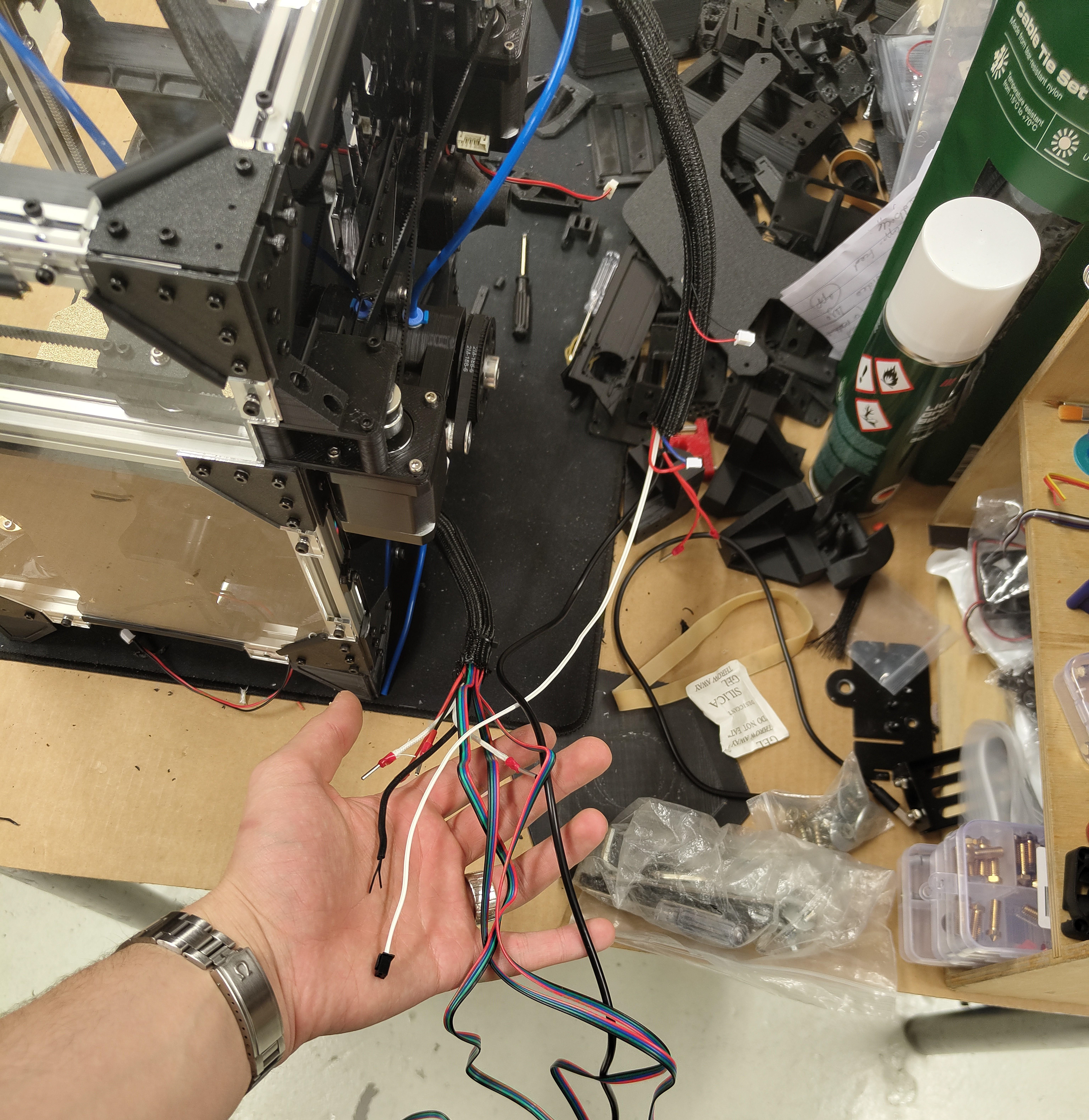
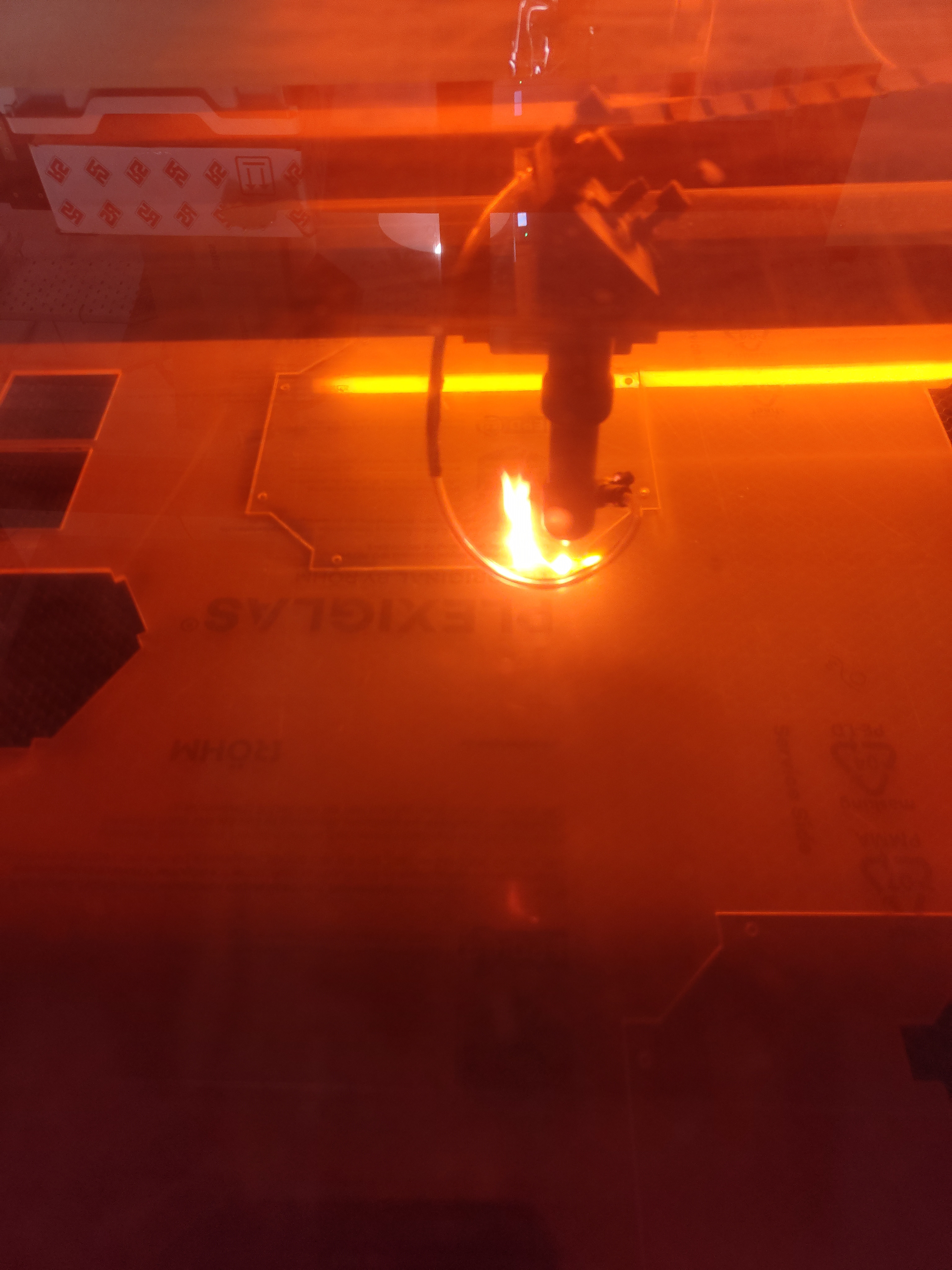
Laser cutting the plexiglass panels
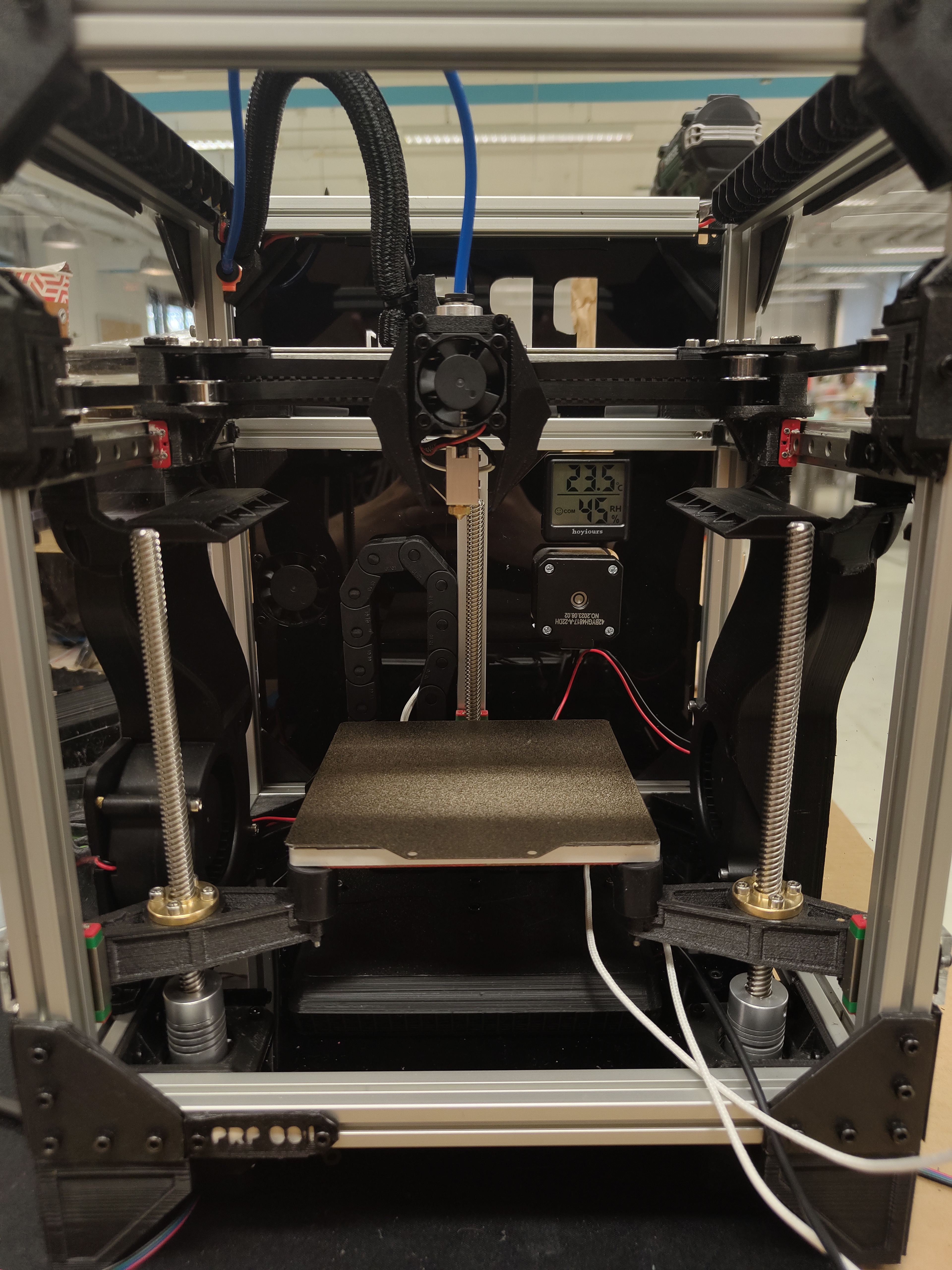
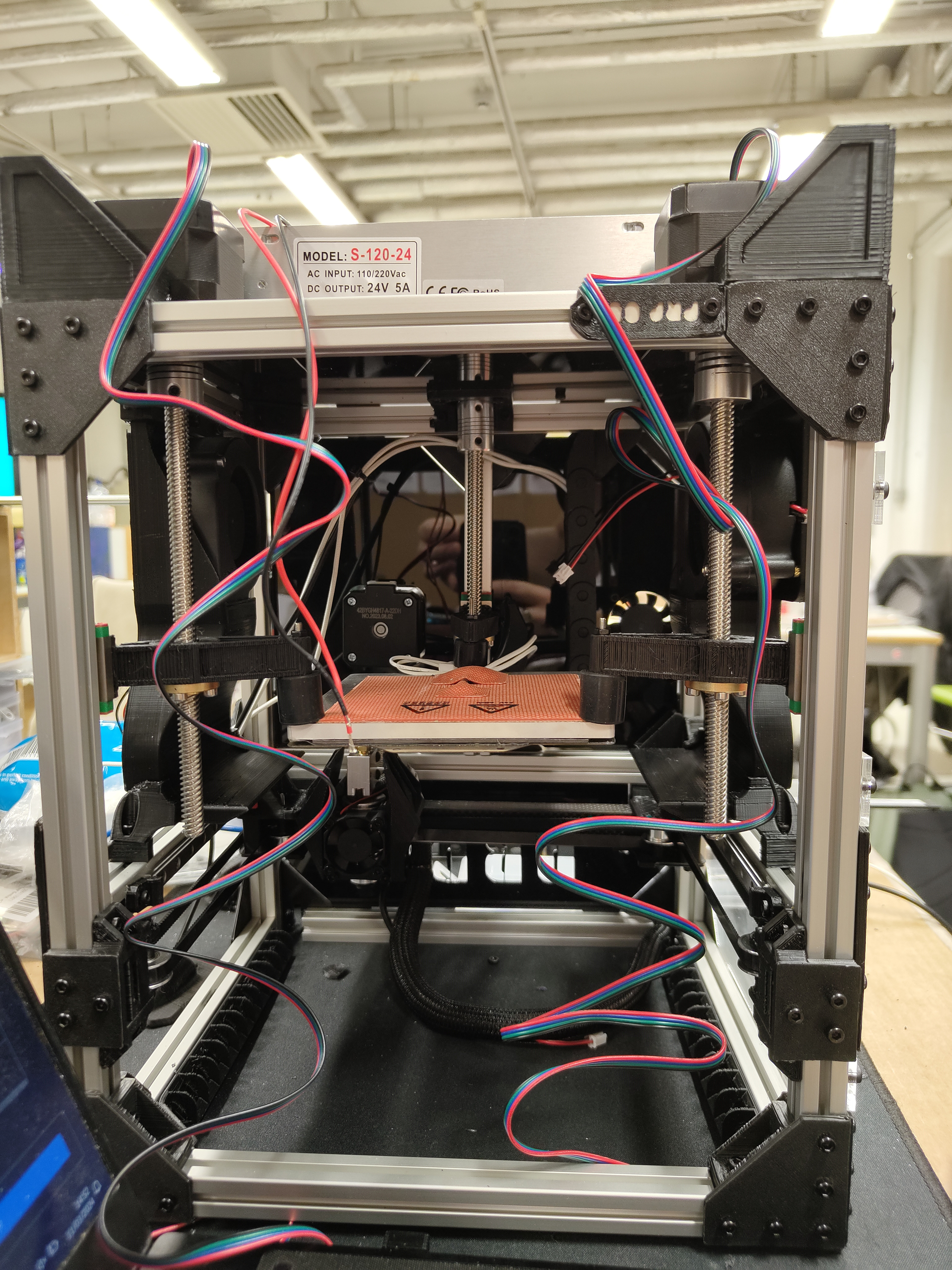
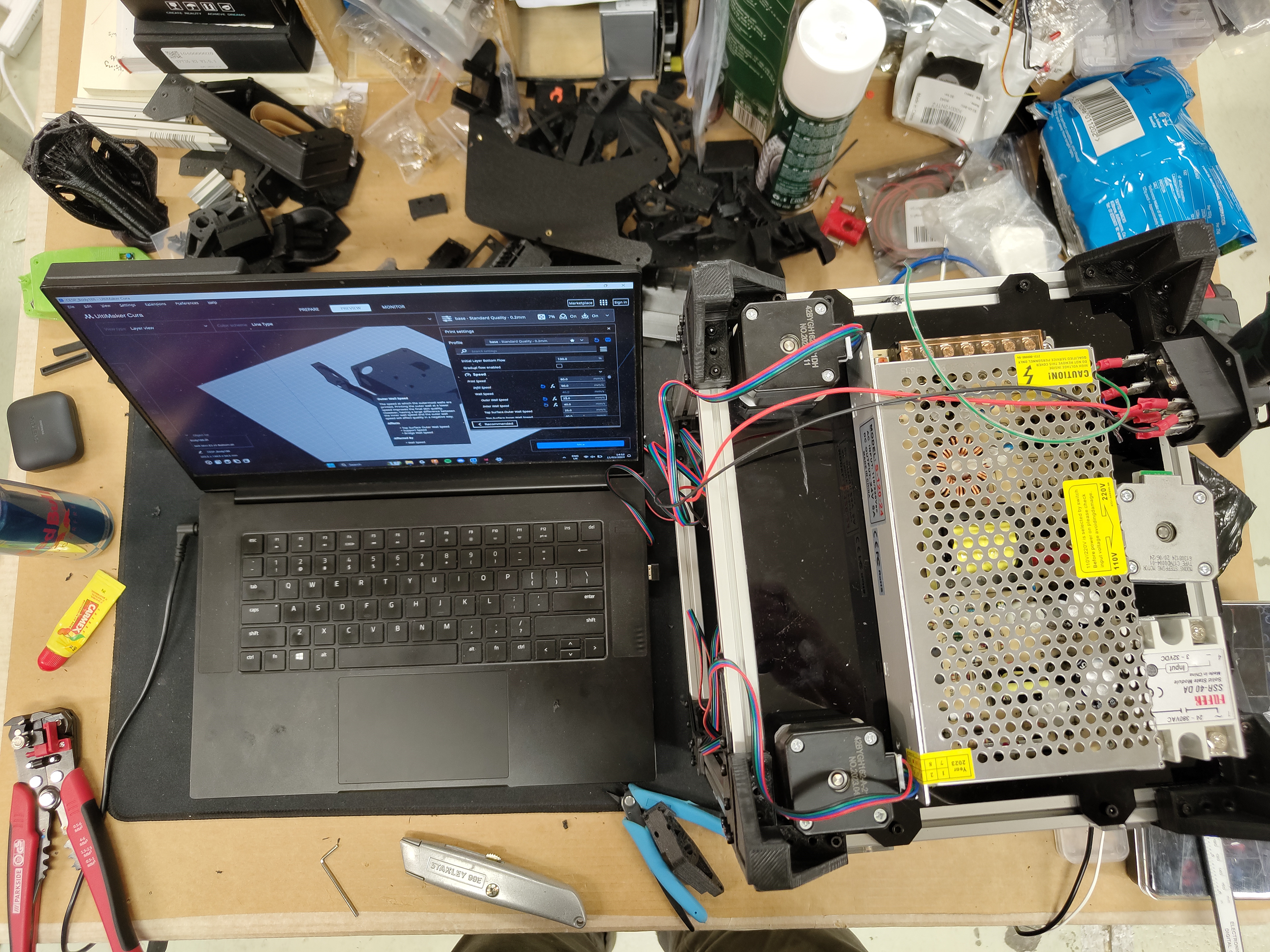
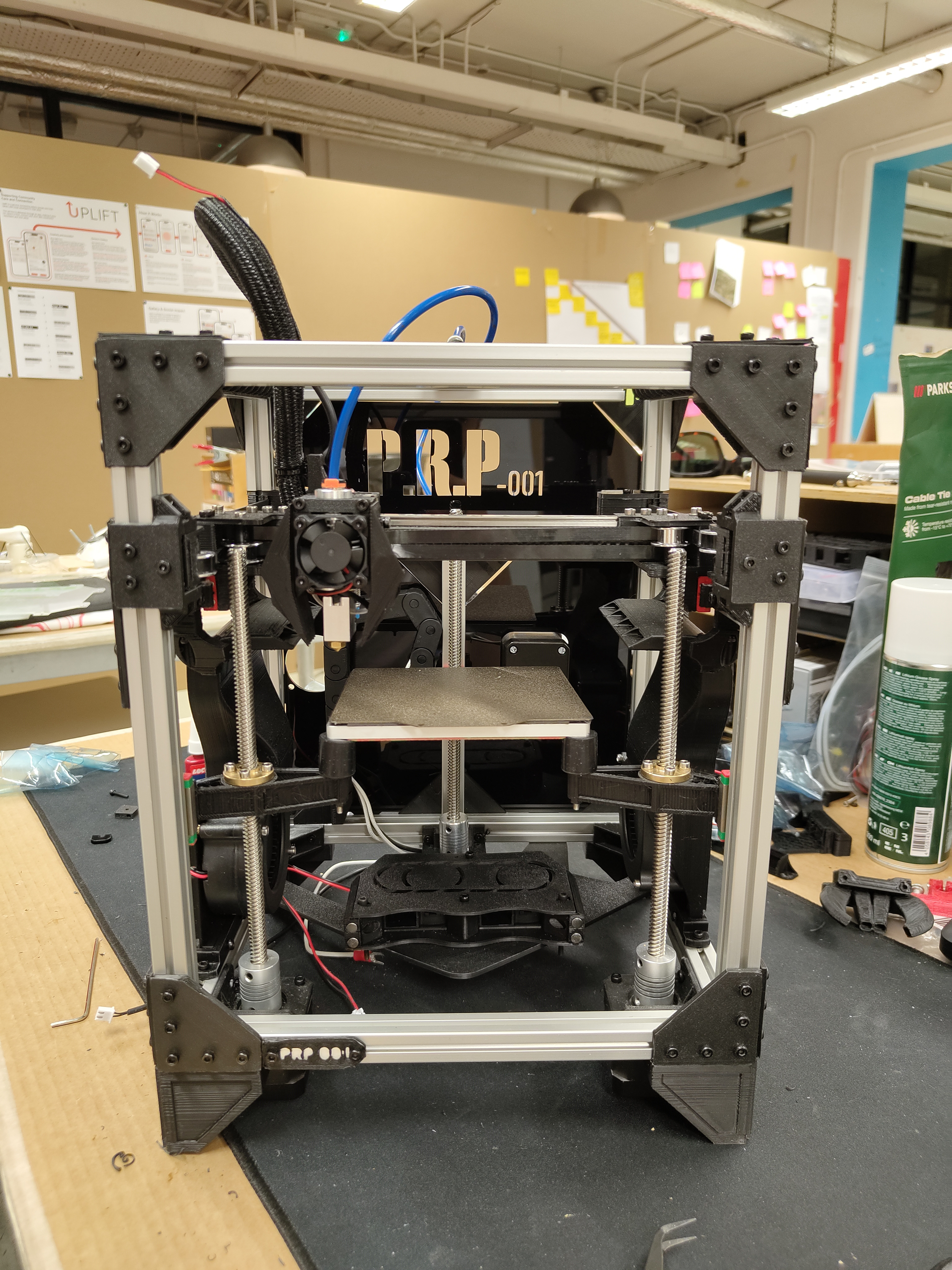
At this point of the project the focus switched to the educational side of the venture, this being doing more work on the instructions and surrounding content, this went through several itterations.
SHown to the right is an example of one of the sub- Assembly instruction sets, there was several of these made to cover the whole printer
tHE AIM OF THESE INSTRUCTIONS WAS TO CONVEY THE KEY OBJECTIVES LEARNED FROM THE USER TESTING SESSIONS, THESE ARE TO SIMPLIFY THE INFORMATION AND GIVE LOTS OF BROKEN DOWN INFORMATIONAL CONTENT.
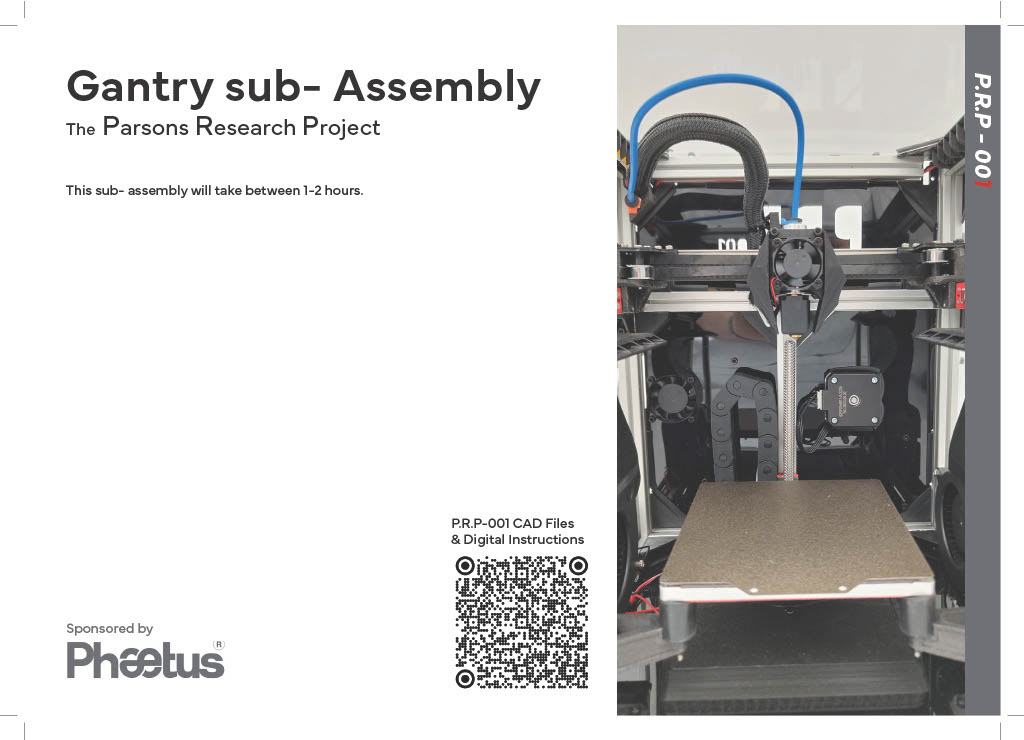

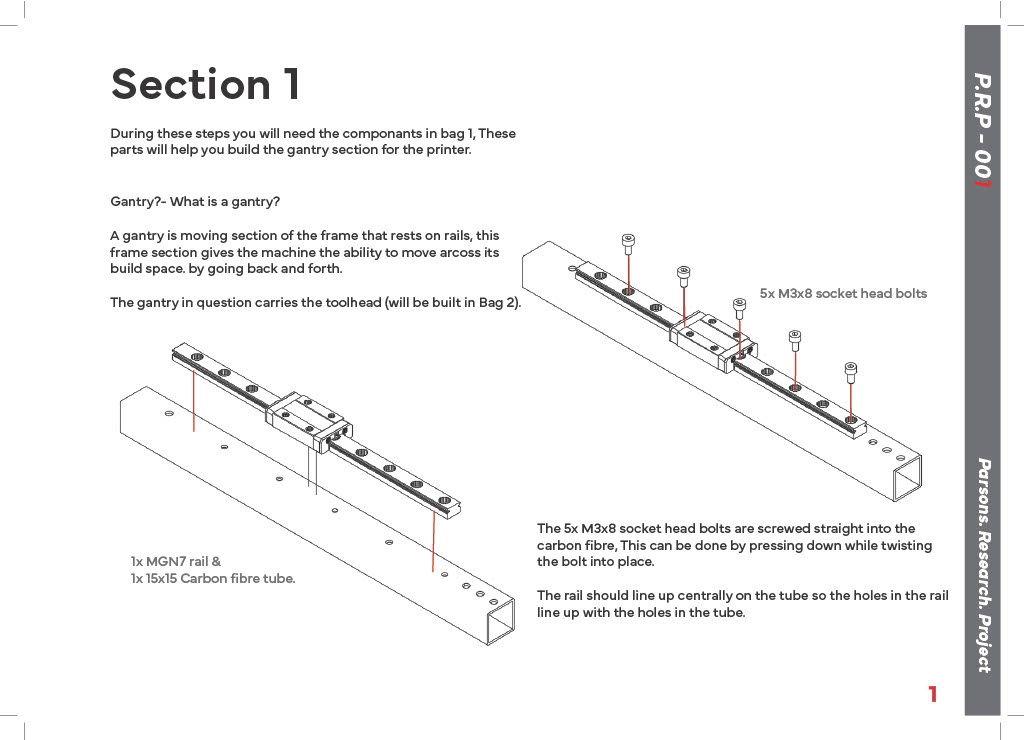
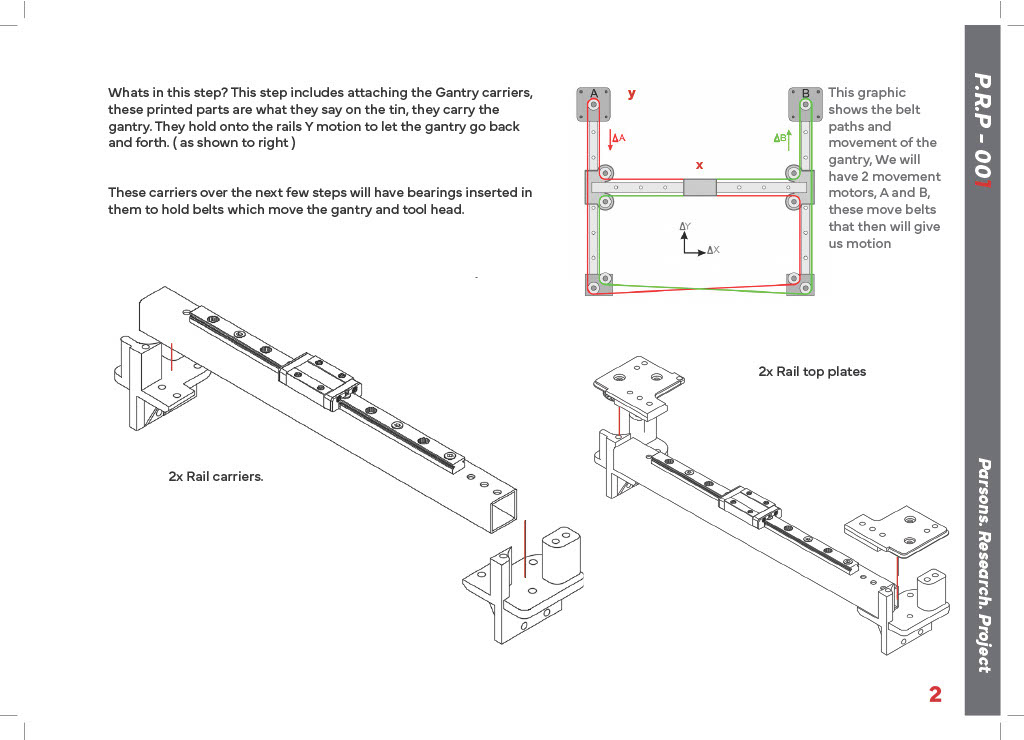
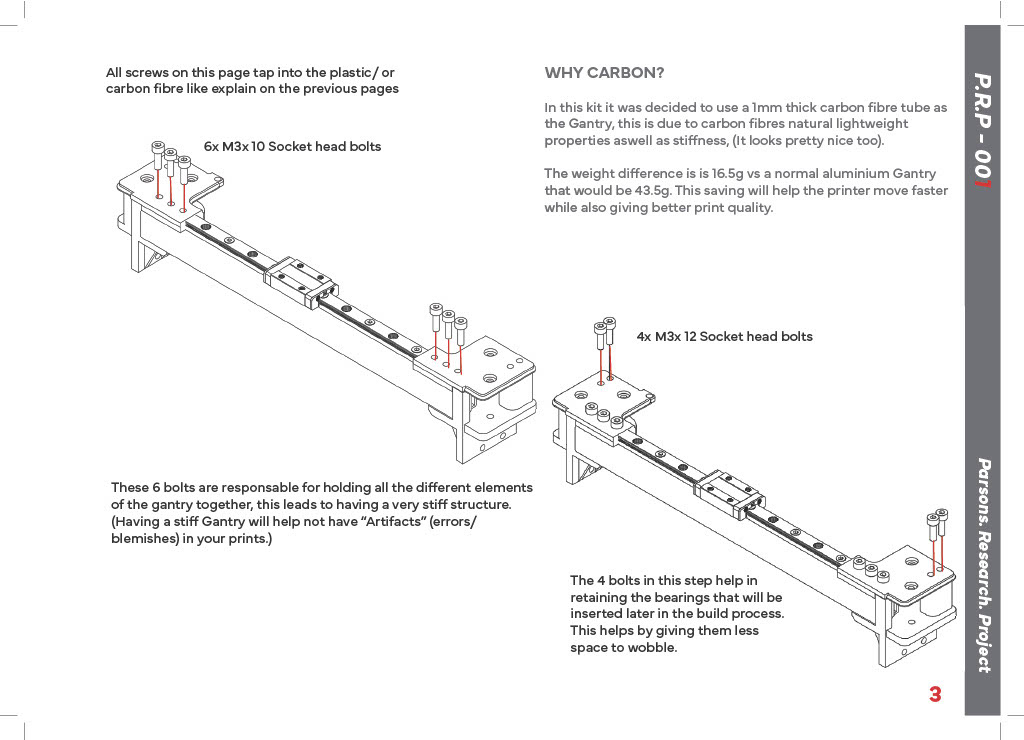
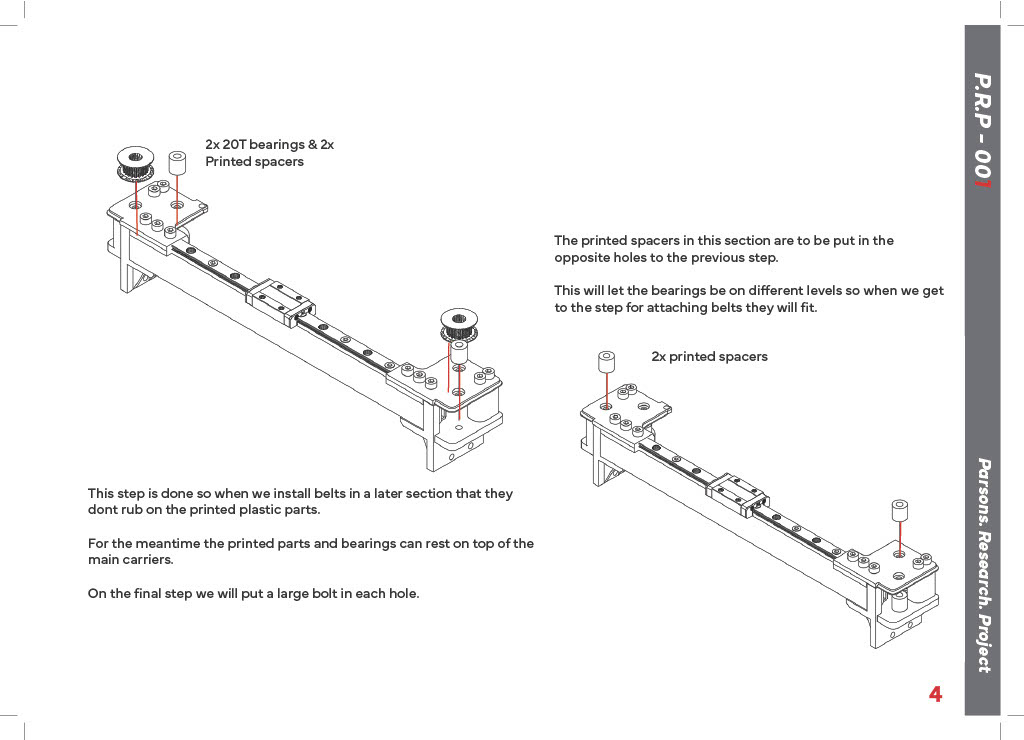
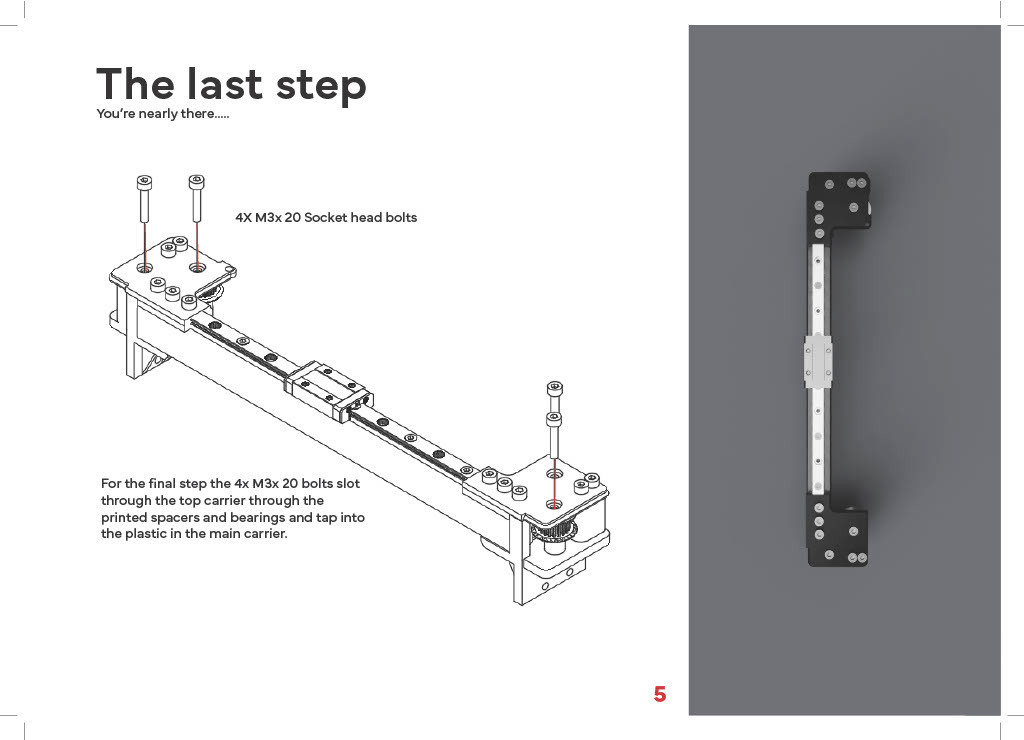
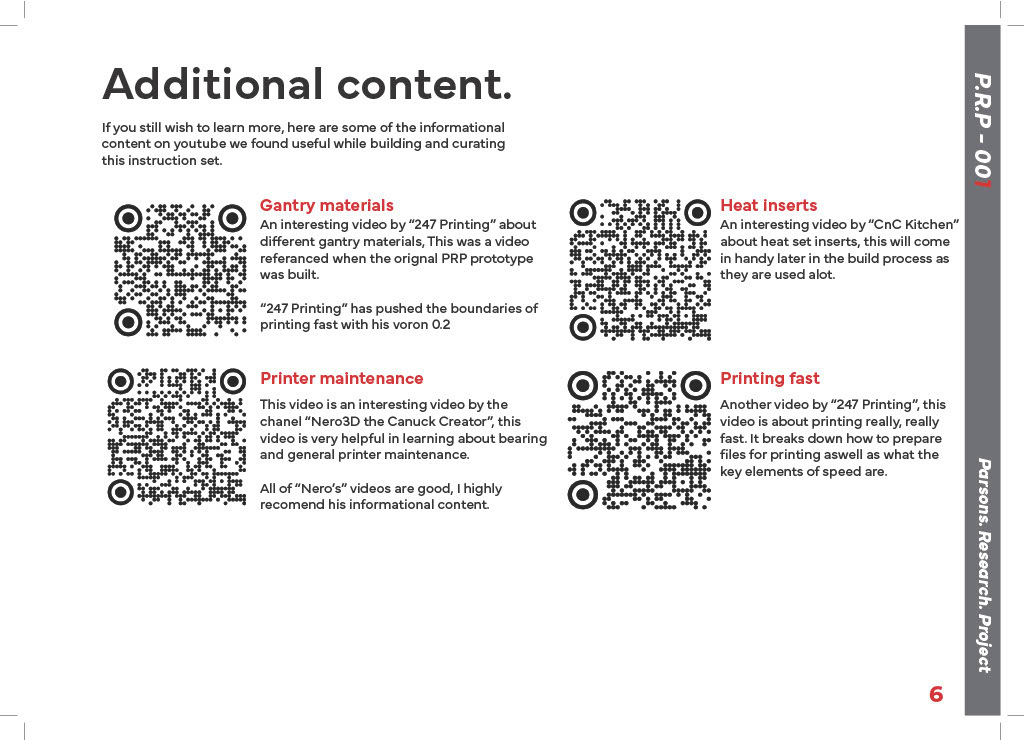
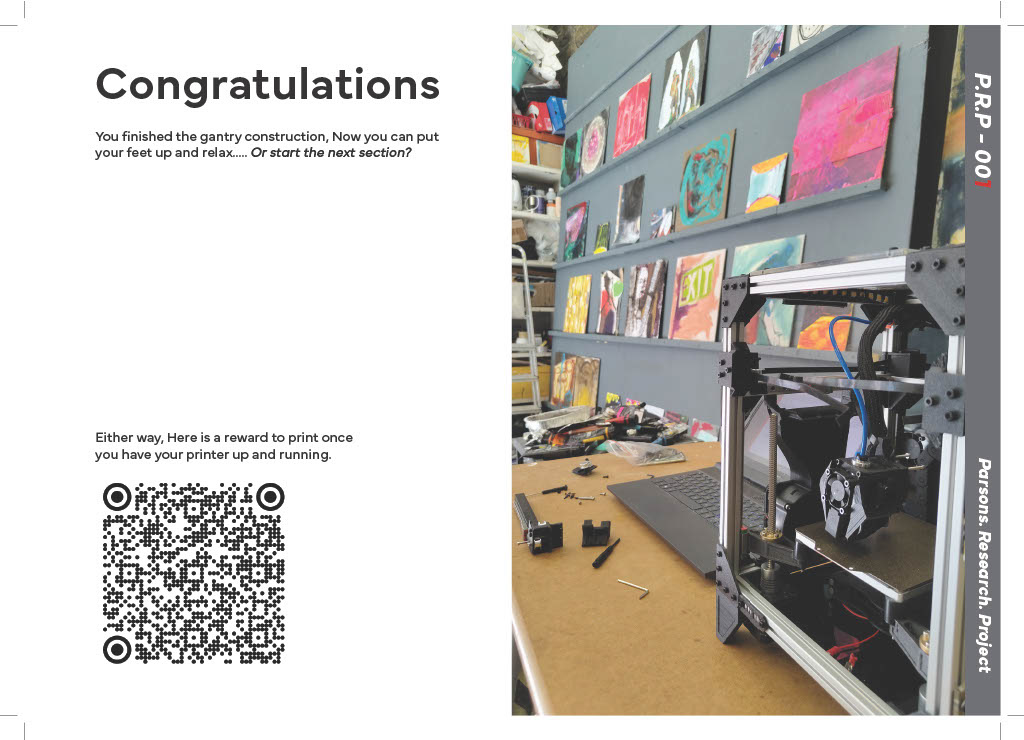
tHEN FROM THERE i finished the physical prototype and completed the project, this rounded off the degree project.
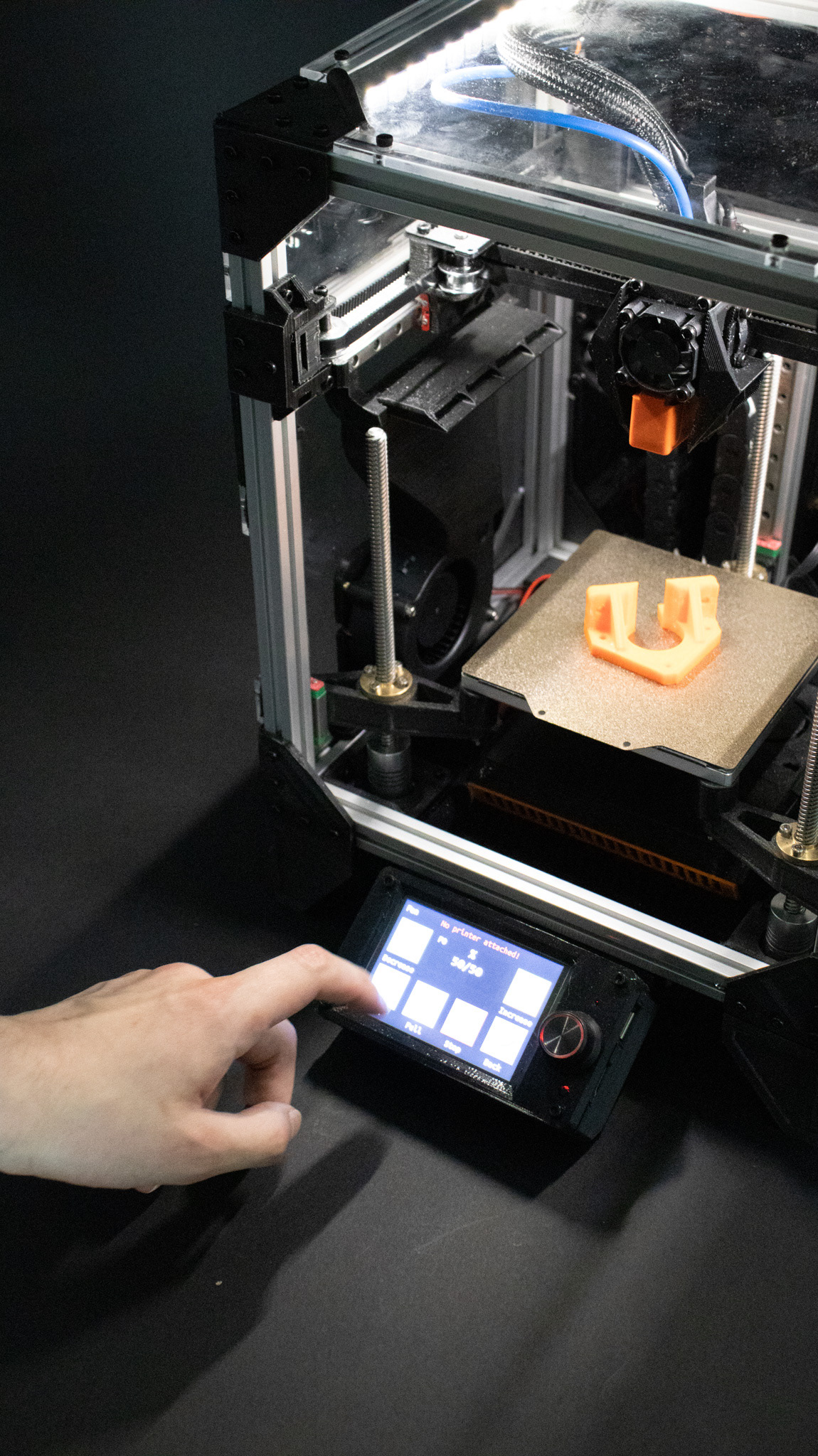
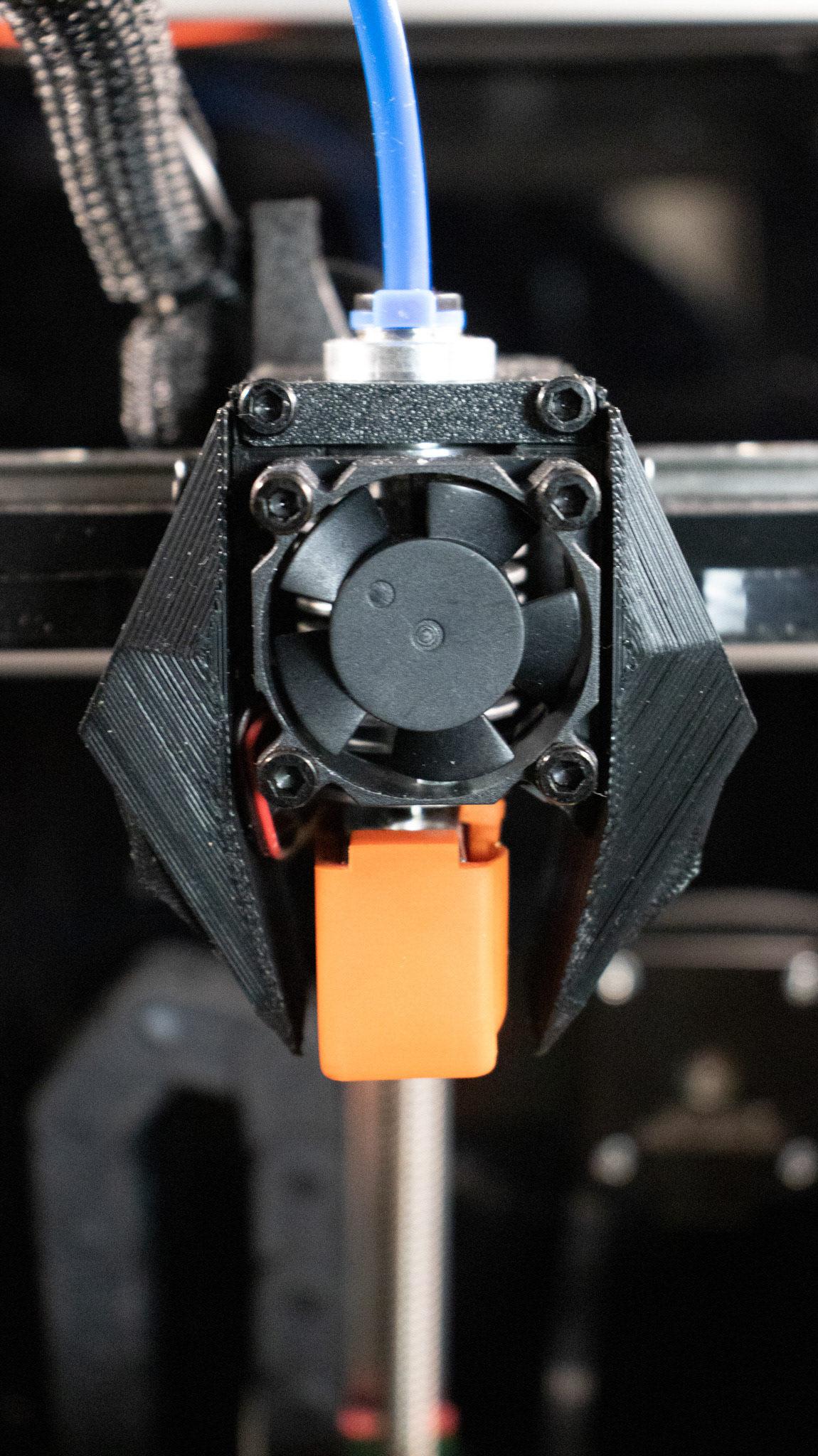
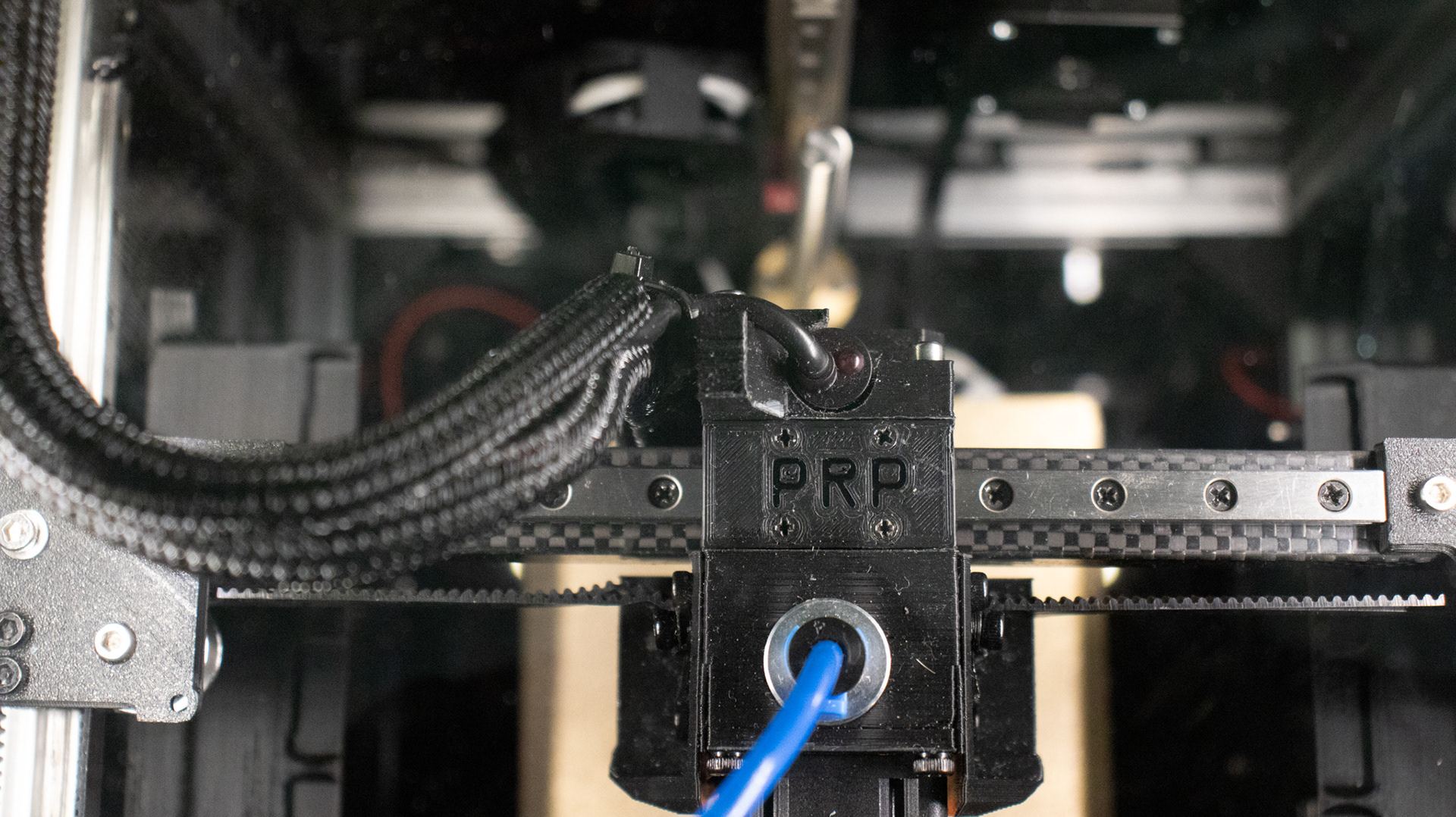

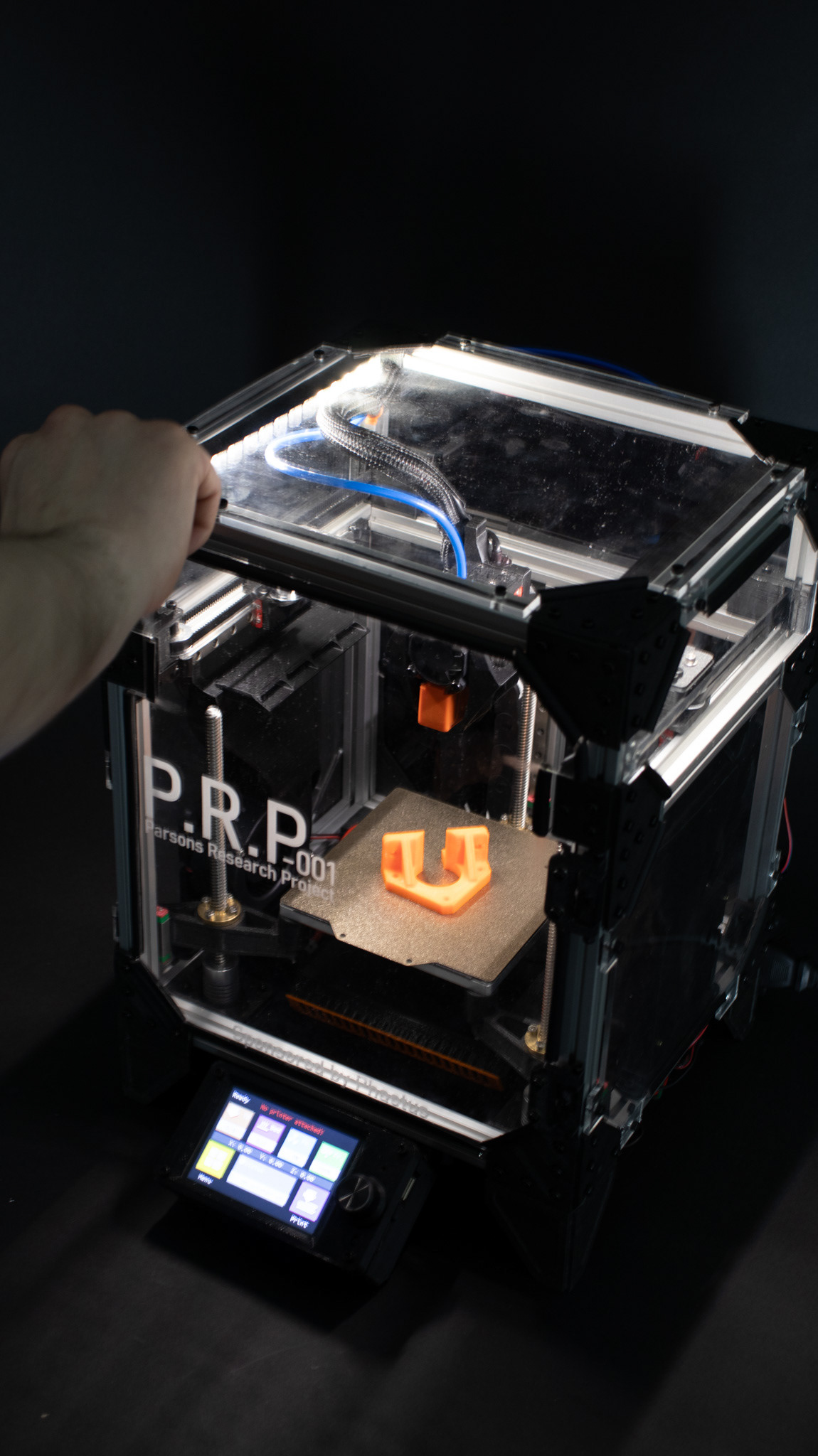
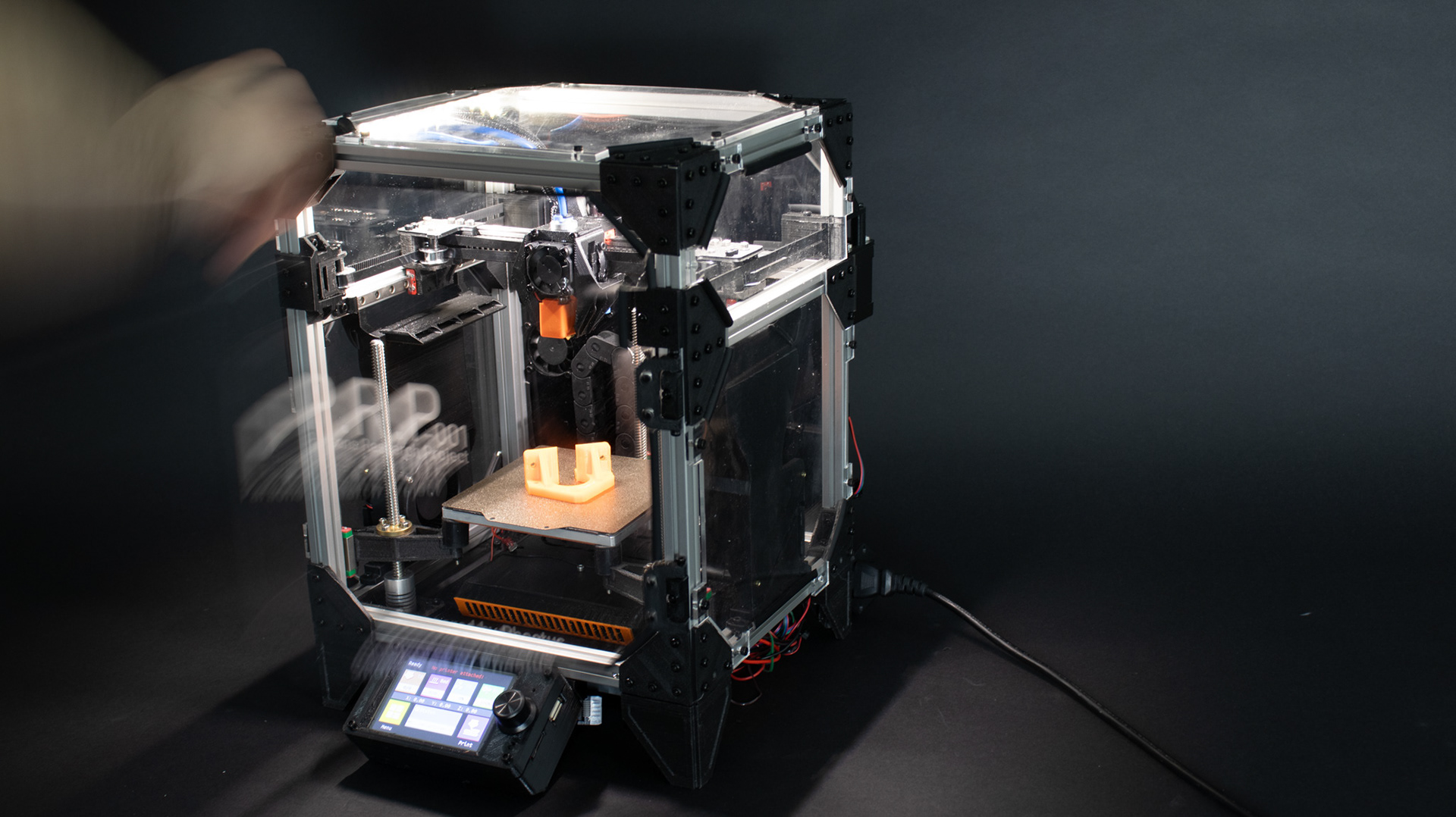
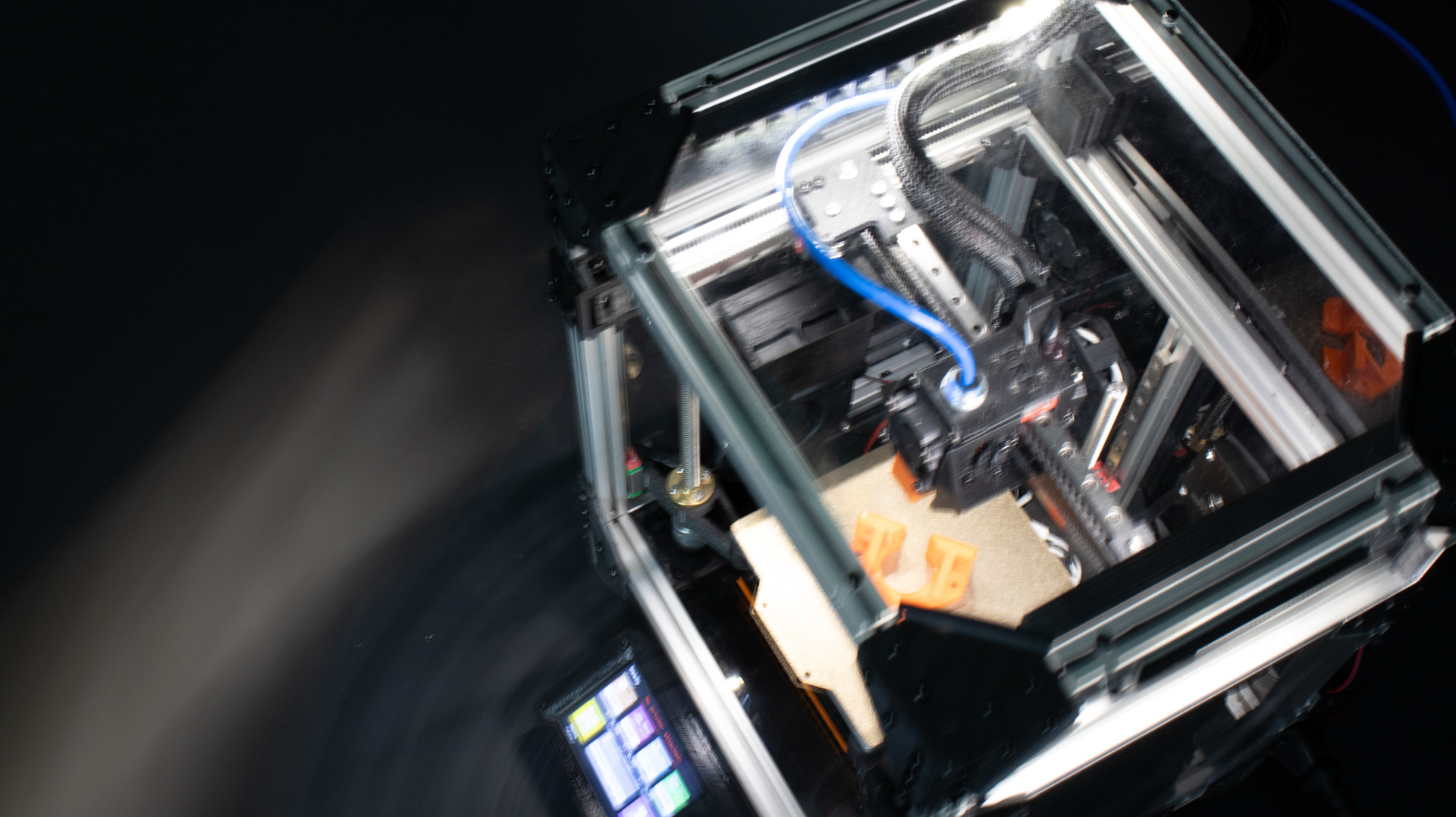
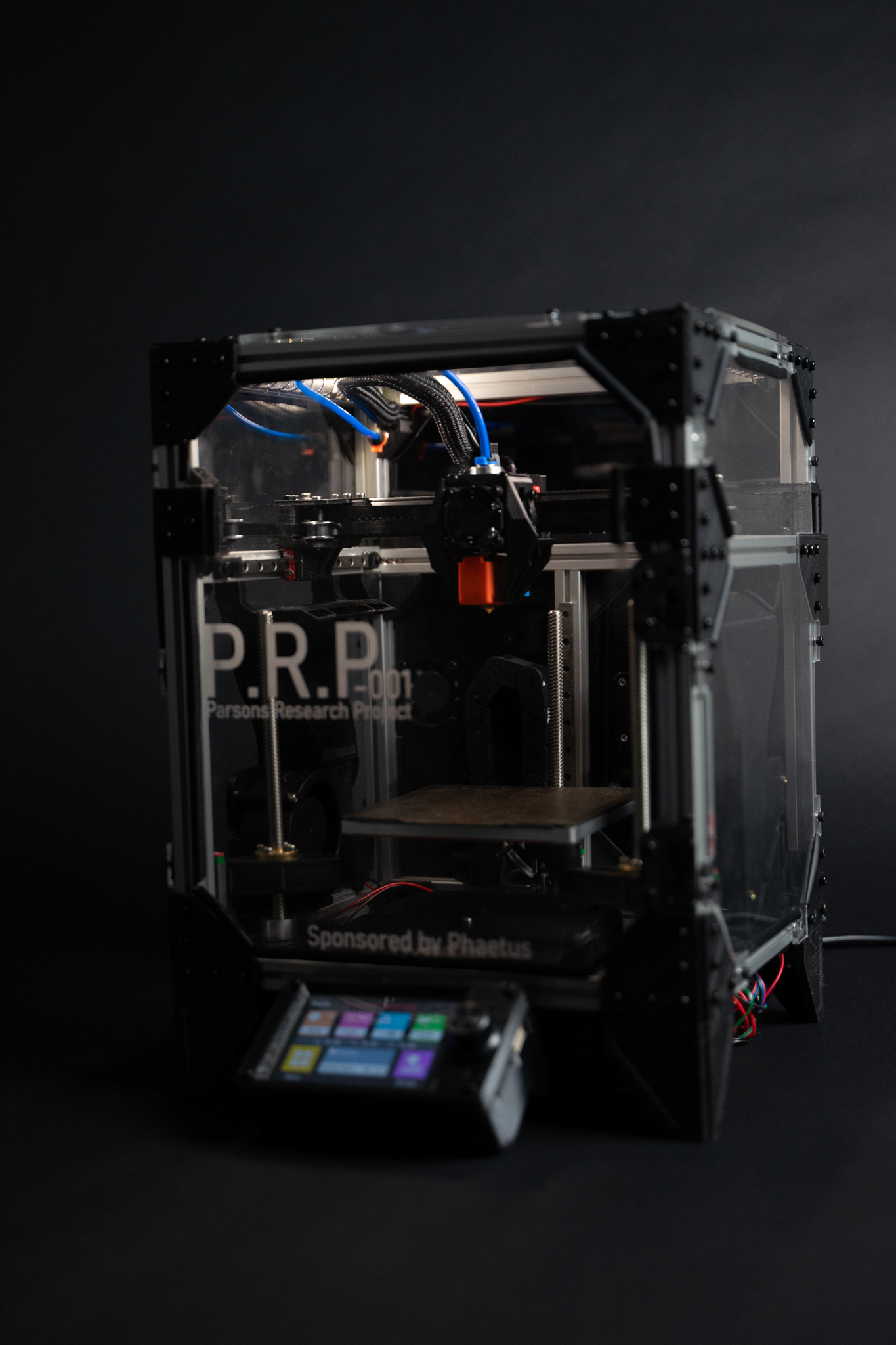
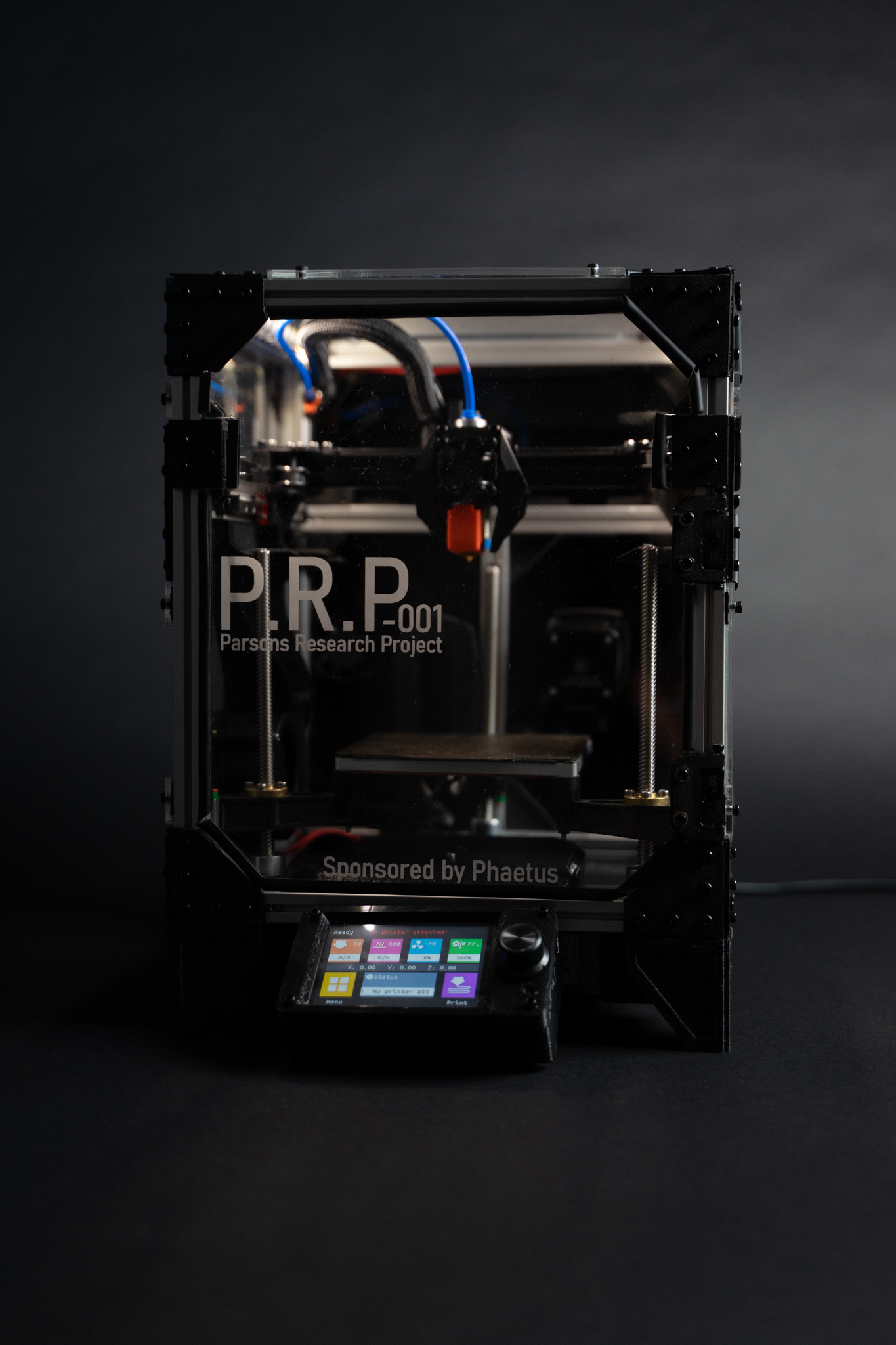
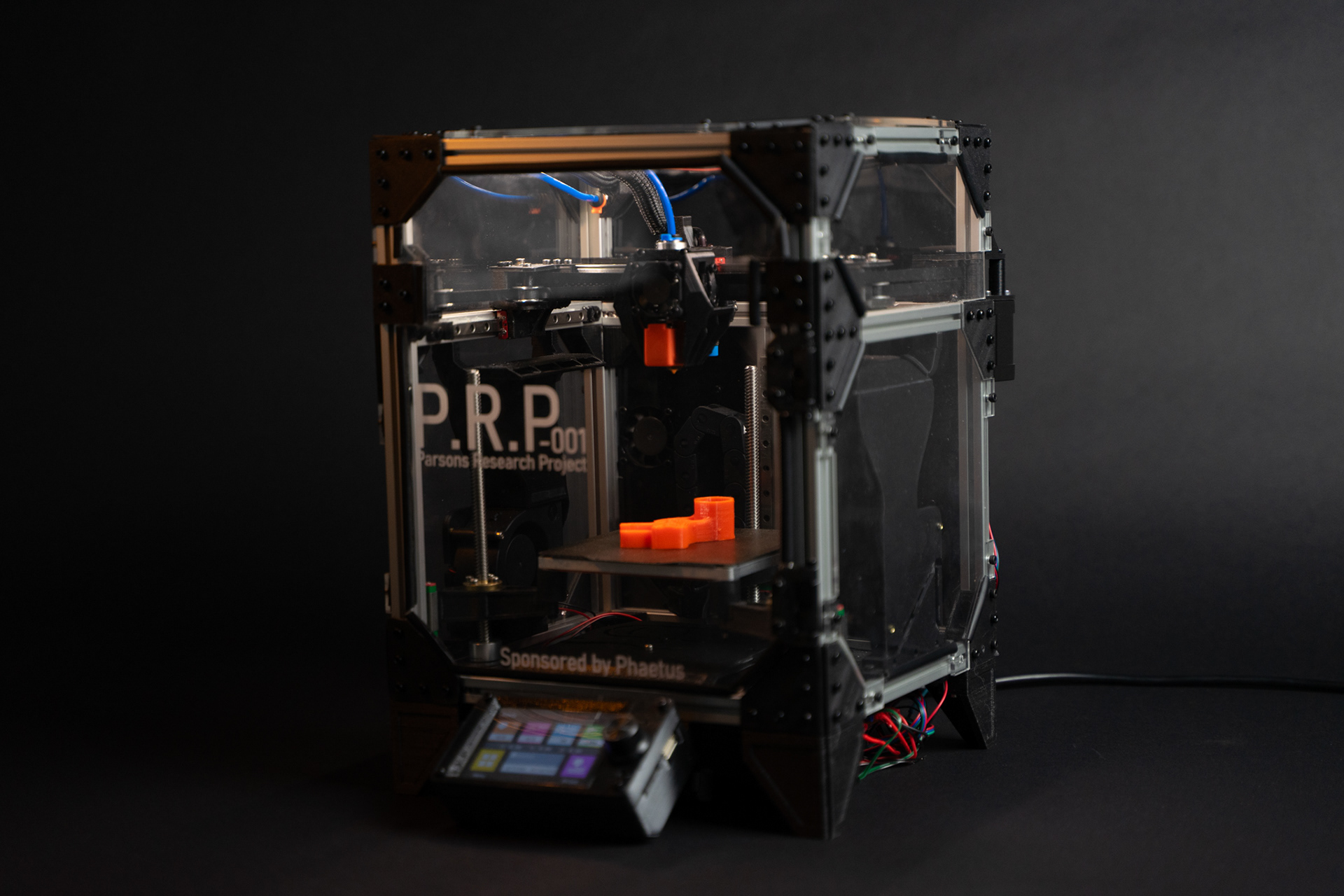
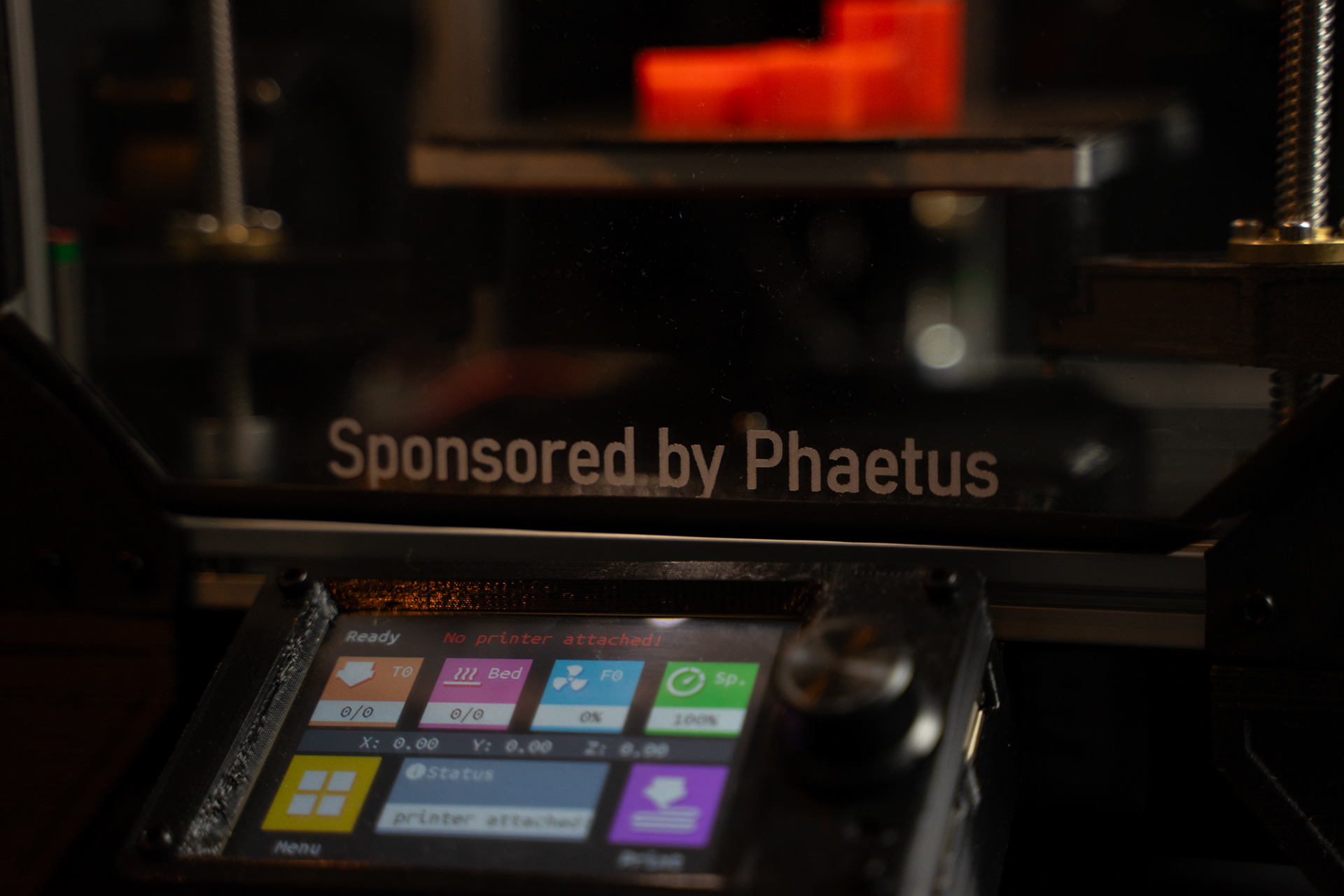
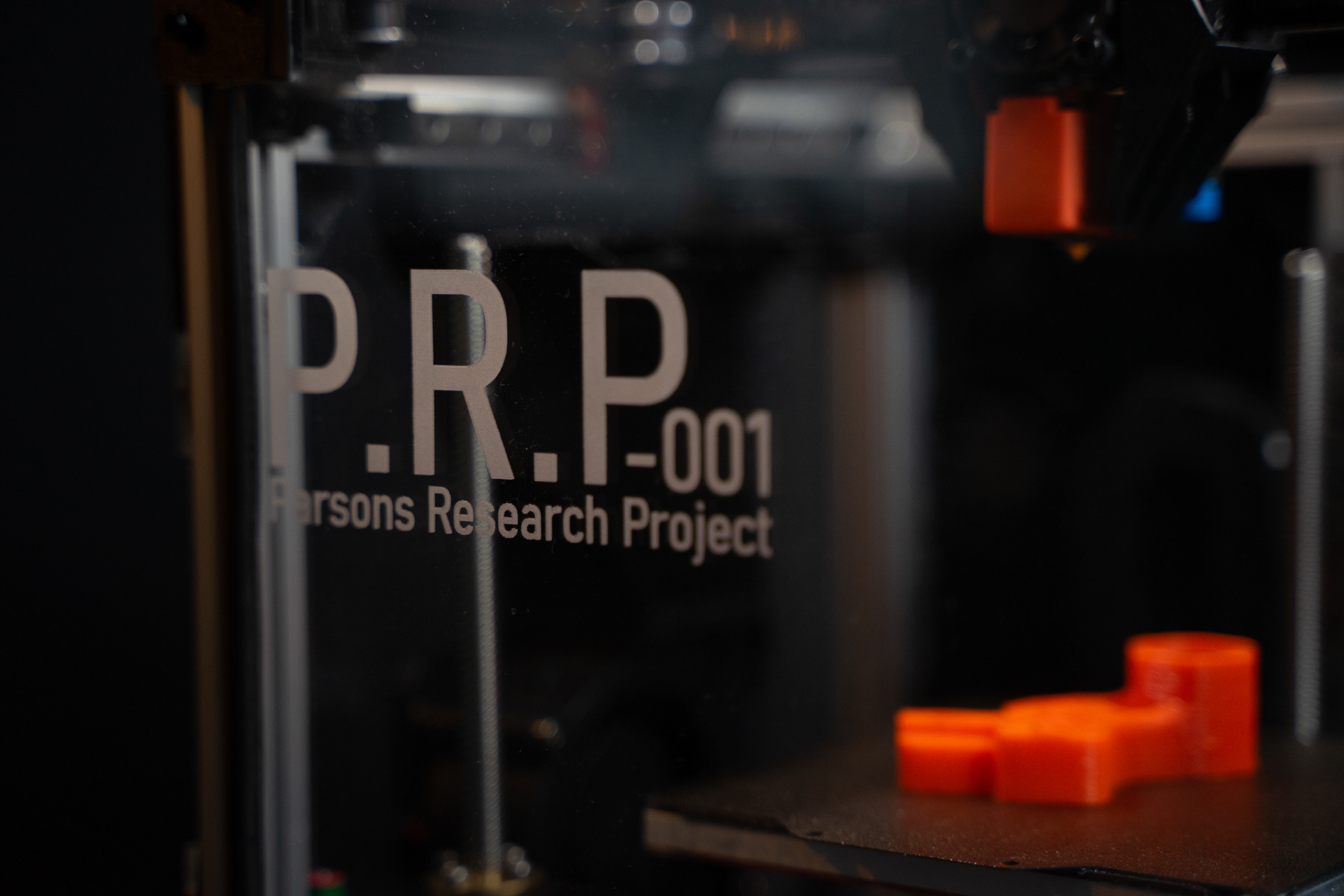
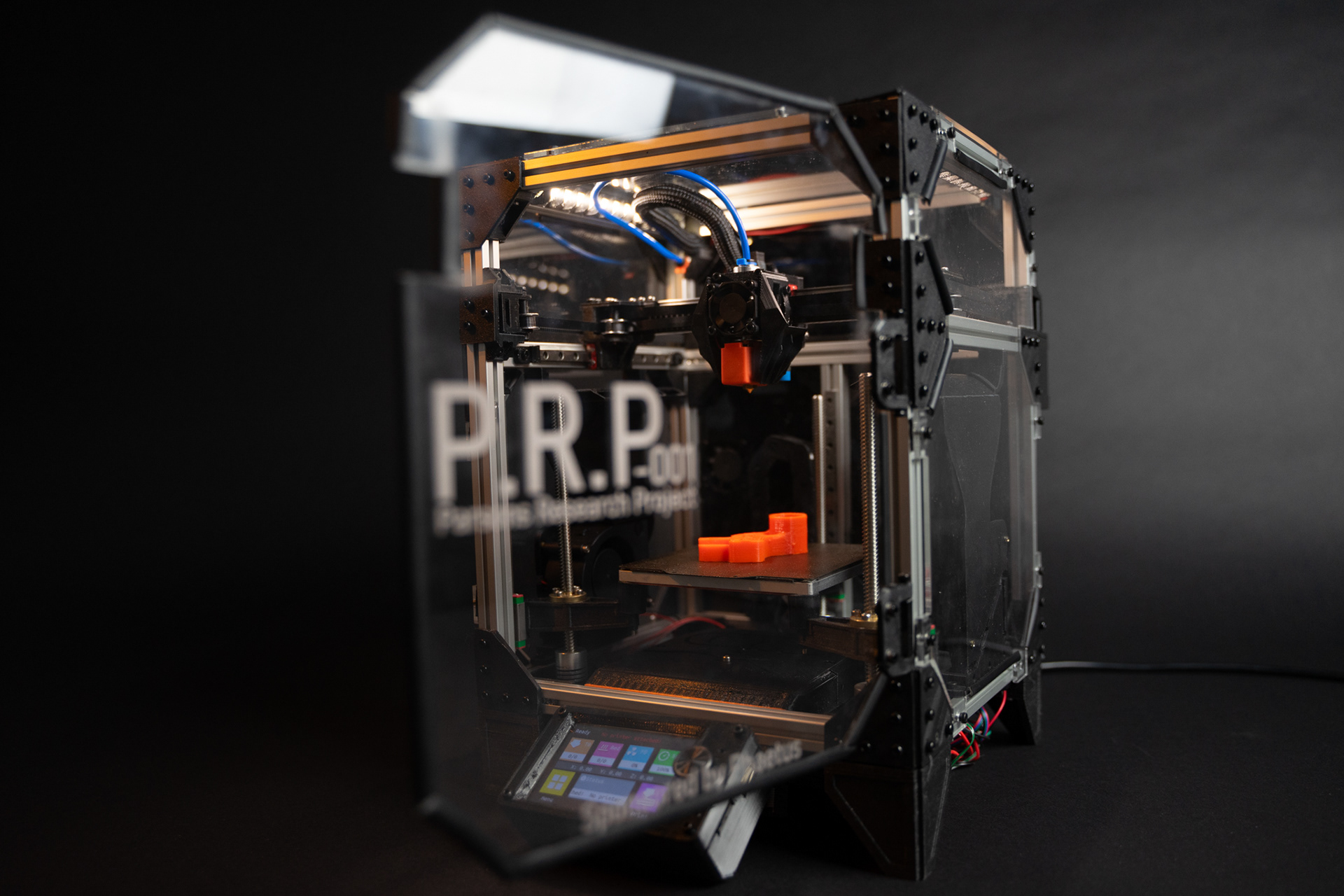
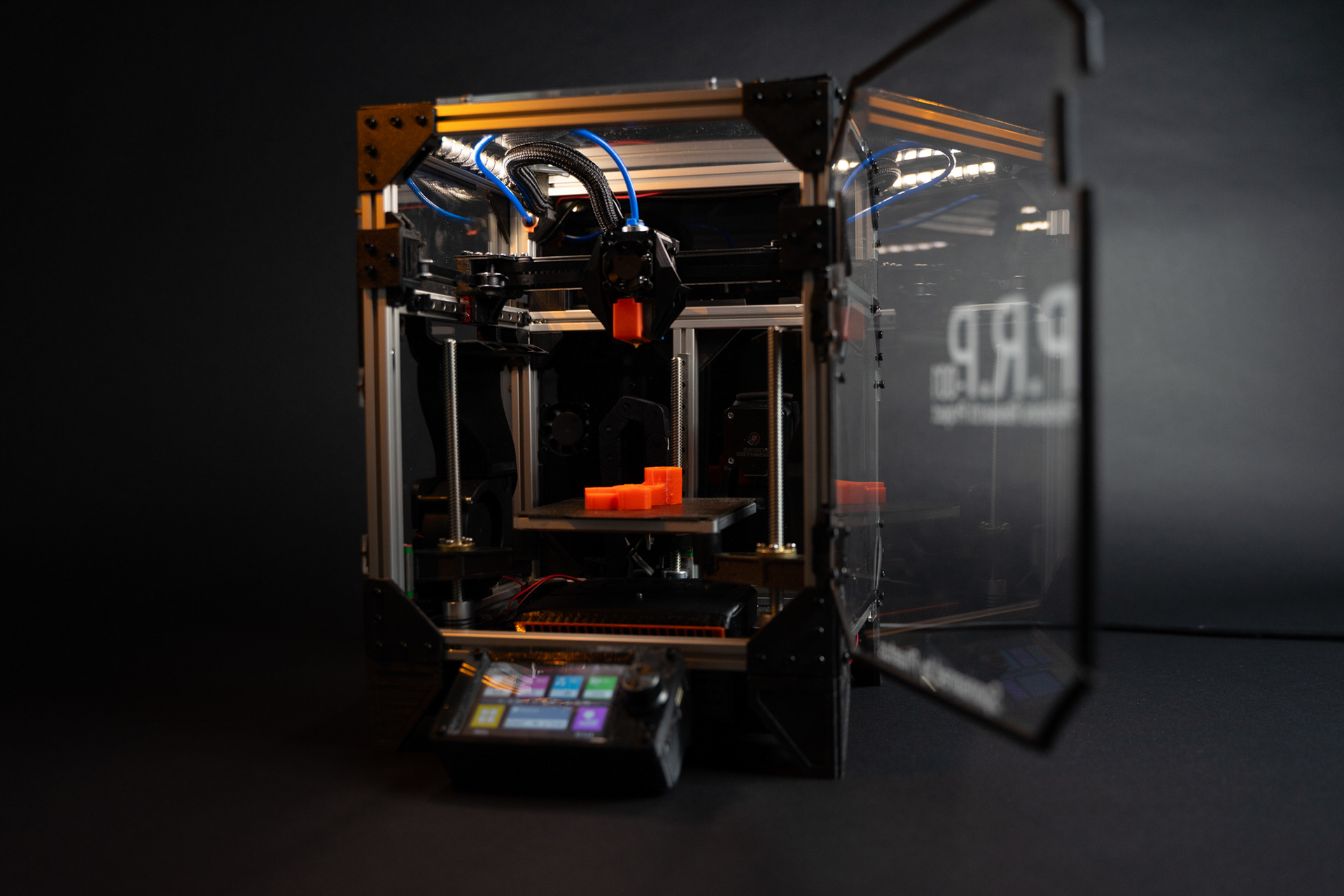
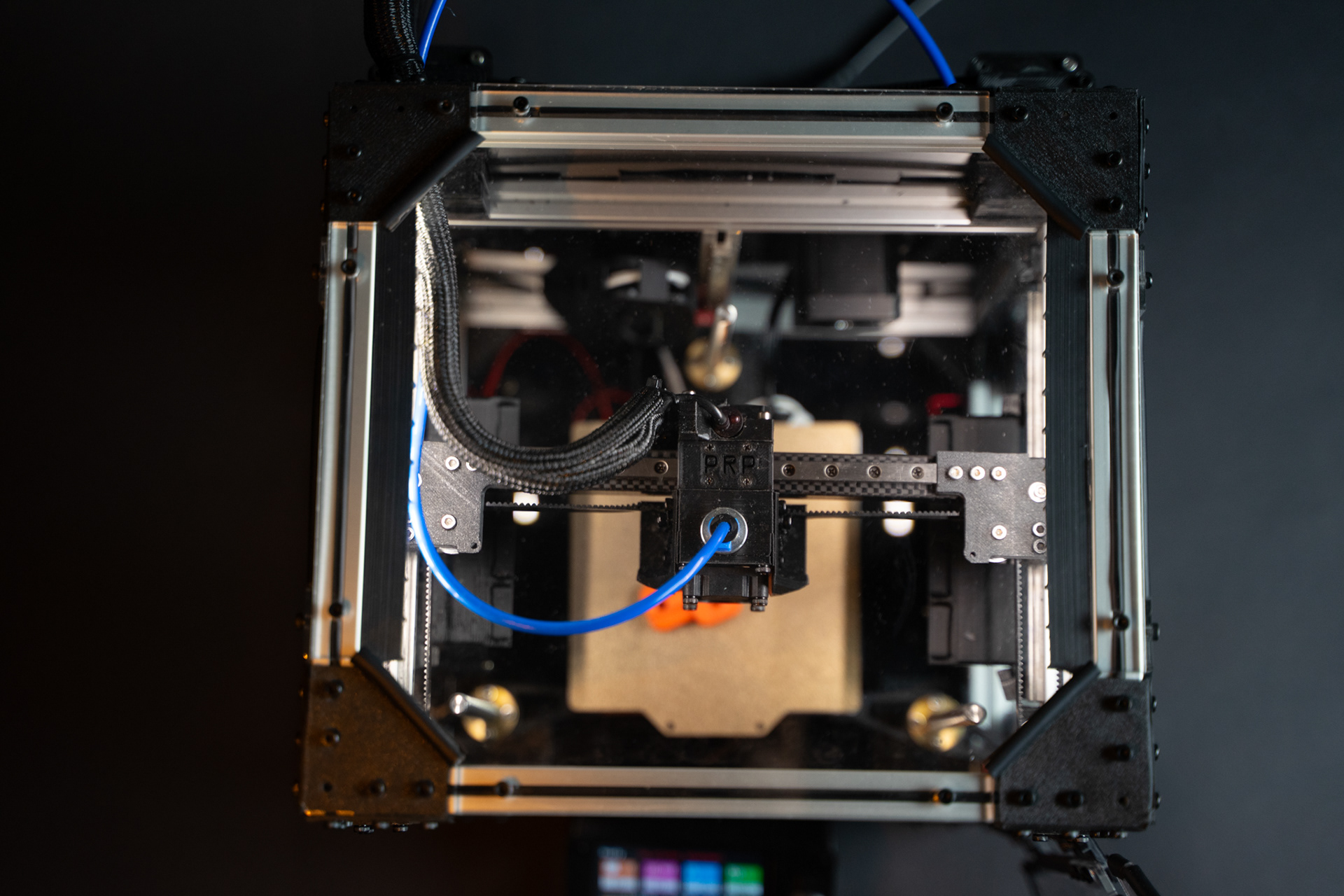
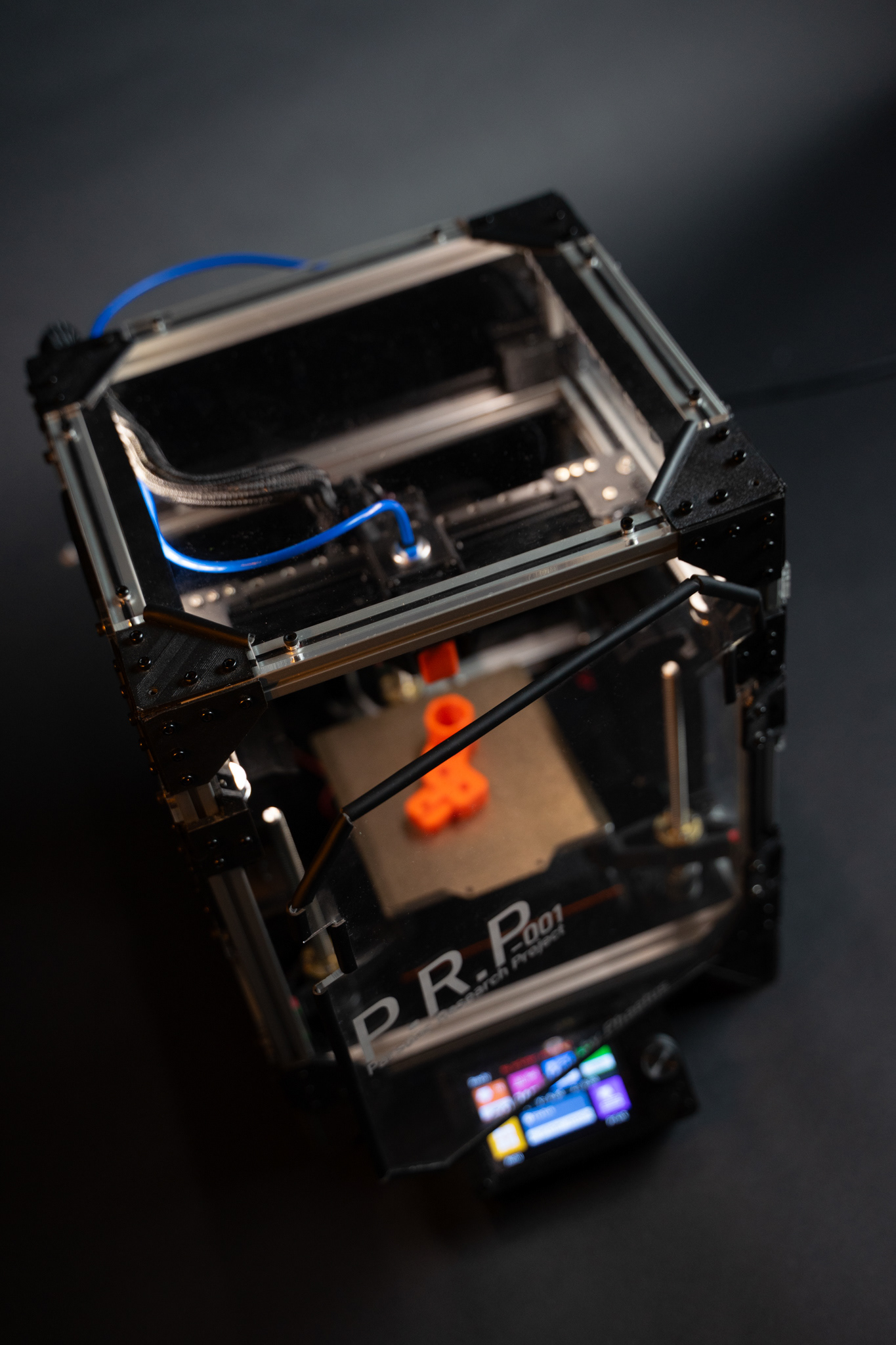
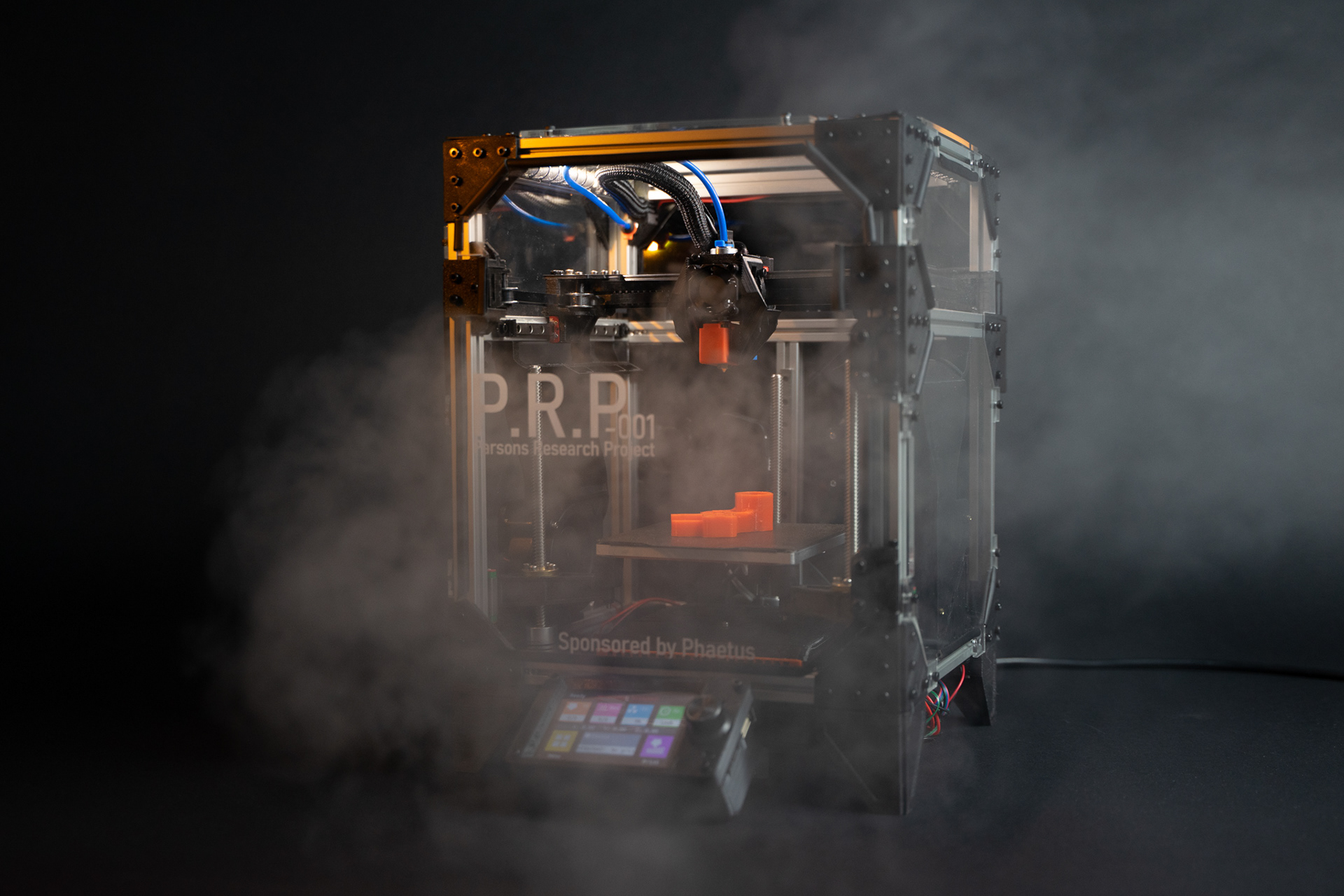
This is the final display at the degree show